This is the place where the majority of the warbird (aircraft that have survived military service) discussions will take place. Specialized forums may be added in the new future
Fri Jul 11, 2014 9:48 am
Kyleb wrote:Scott, how do you cut your PVC forms to leave the clean edges? I've never cut PVC sheet, but I tend to get fuzzy edges whenever I cut PVC pipe, UHMW, or most any plastic.
I cut on a band saw and yes, get the fuzzies. I then hand sand with 220 paper to smooth out the saw marks as they can transfer to the soft material. I use a router to give the radius I want for the form. This stuff is great. Once you try it, you'll never go back to MDF.
Tue Jul 22, 2014 2:00 am
Scott,
"same old" is good. Never get tired of looking at your work. Thanks for taking the time to post them.
Mac
Tue Jul 22, 2014 4:41 pm
Excellent work as always!
Tue Jul 22, 2014 6:28 pm
Agree with the posters above. There's no such thing as "same old" with your stuff. Part of the fun is seeing how once you make the part(s) is how you then make others if needed and then they all go together.
It gives me more motivation to start learning how to do some of this stuff because while I know it'll take a lot of time and practice to even get half as good as you, it seems like a skill that might come in handy if I want to keep hanging around airplanes.
Tue Jul 22, 2014 11:07 pm
Thanks to all for the kind comments. This really is not that difficult if you guys actually try some simple pieces. It really is 40's technology combined with a few years of knuckle busting and a little blood.
To finish the last pieces shown, the flow forming actually stretches the bent over flange a little which curves the part along the plane of the three "flags". Now, I don't want to make a lot of marks on the piece and even though it is .062" material, it is dead soft so it will move very easily. I also have left what I think to be a considerable amount of stock to trim when we fit to Bu 92050 so I want to concentrate the shrink to an edge I hope to trim off eventually. So. I'll straighten them gently now, then check again after heat treating. I will make any corrections necessary prior to the age hardening process after heat treat then they will be set.
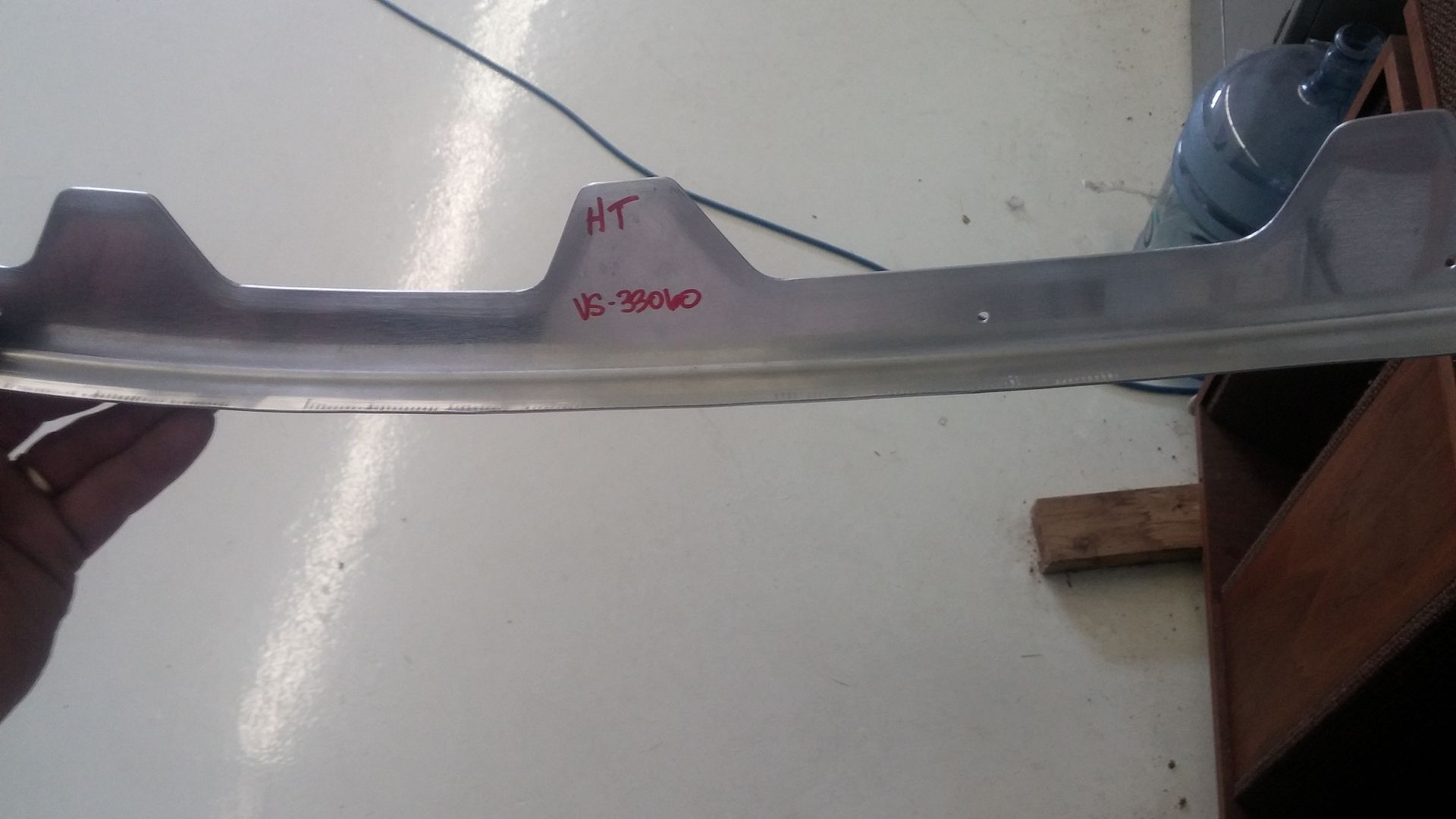
Wed Jul 23, 2014 10:45 pm
Tue Aug 12, 2014 11:03 pm
Regrouping after great week at Oshkosh. Will continue shortly. Thanks to the great folks I met who are legends in Warbird restoration.
Wed Aug 13, 2014 6:13 am
Awesome cant wait to see some more metal munching..
Sat Aug 16, 2014 9:16 pm
Scott,
A real pleasure to see your work. Any chance of some video of the action?
PC
Sat Aug 16, 2014 10:09 pm
Funniest home video type or what? I've done a couple of flow forming some of these parts. Let me know what you are looking for and if I can accommodate perhaps we can.
Thanks for the support.
Sat Aug 16, 2014 10:52 pm
So, sorry for the time off from posting but it was OSH!
Going back to the VS-33060 from above, there is a companion piece VS-33061. These are the outer edge formers for the lower sections. Since the contours are the same, I used and modified the "33060" tooling since they have been completed. The pieces are flow formed into a curved channel. They then get a turned lip for strength. Here is the lip turn and am using a small rawhide to do the edge.
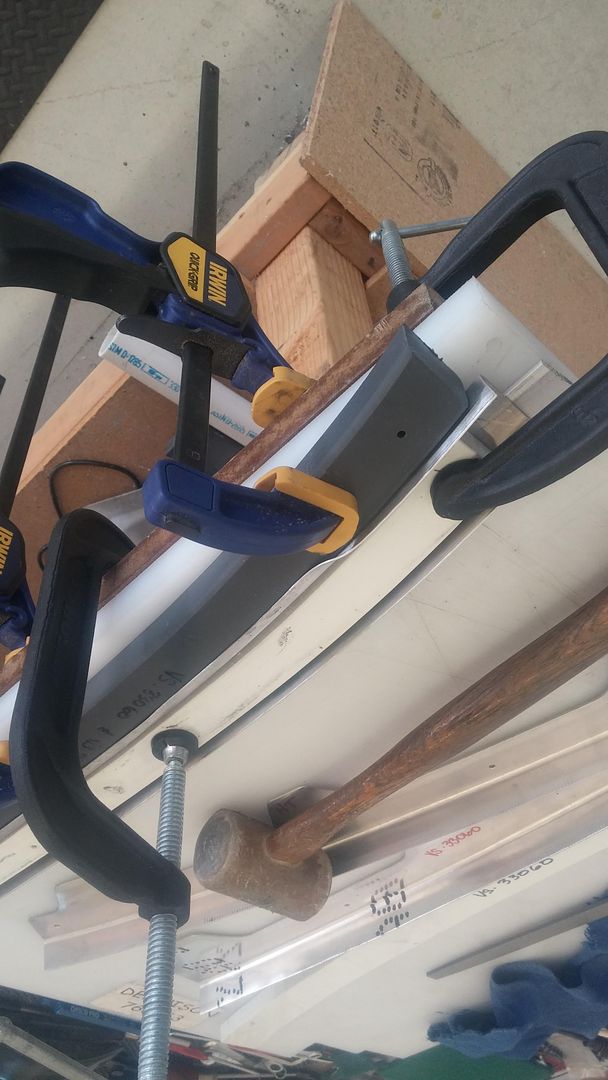
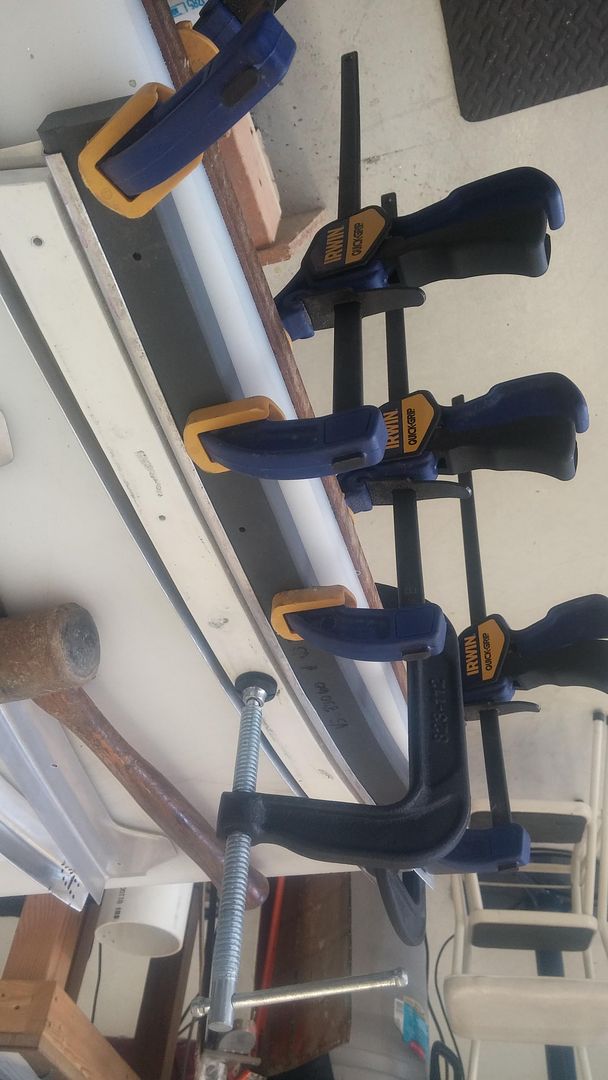
Still need final trimming.

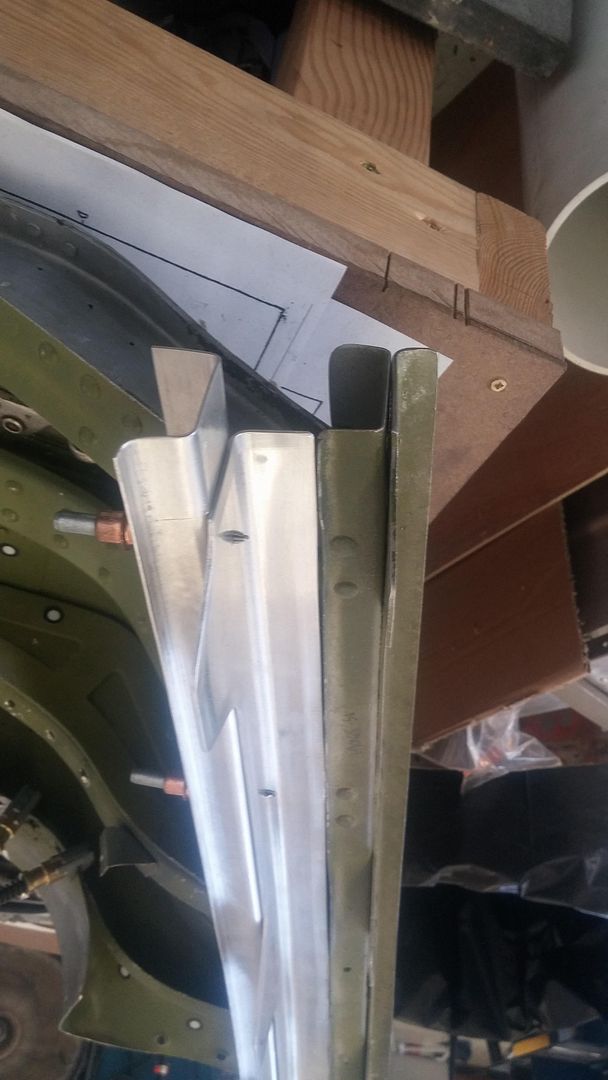
The matched set.
Sat Aug 16, 2014 11:04 pm
I was recently asked to help out with a vertical stabilizer for a "rotary wing" aircraft, Schweizer TH55A trainer. This is the one to be recreated and the tail boom is 6" diameter so I used some 6" PVC pipe as a fixture.
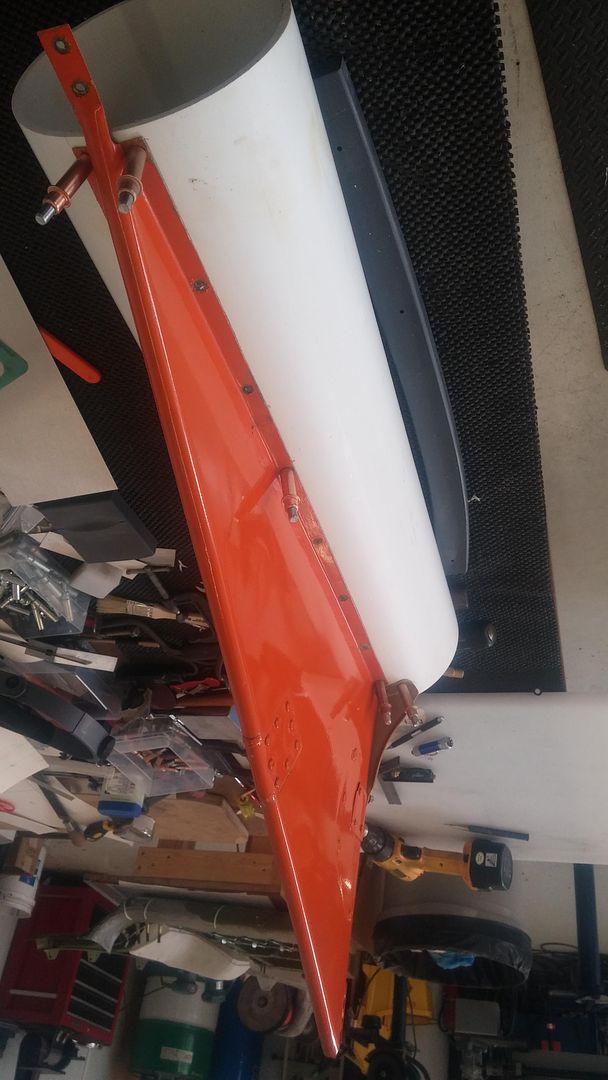
The doublers and extra rivets are from prior fixes.
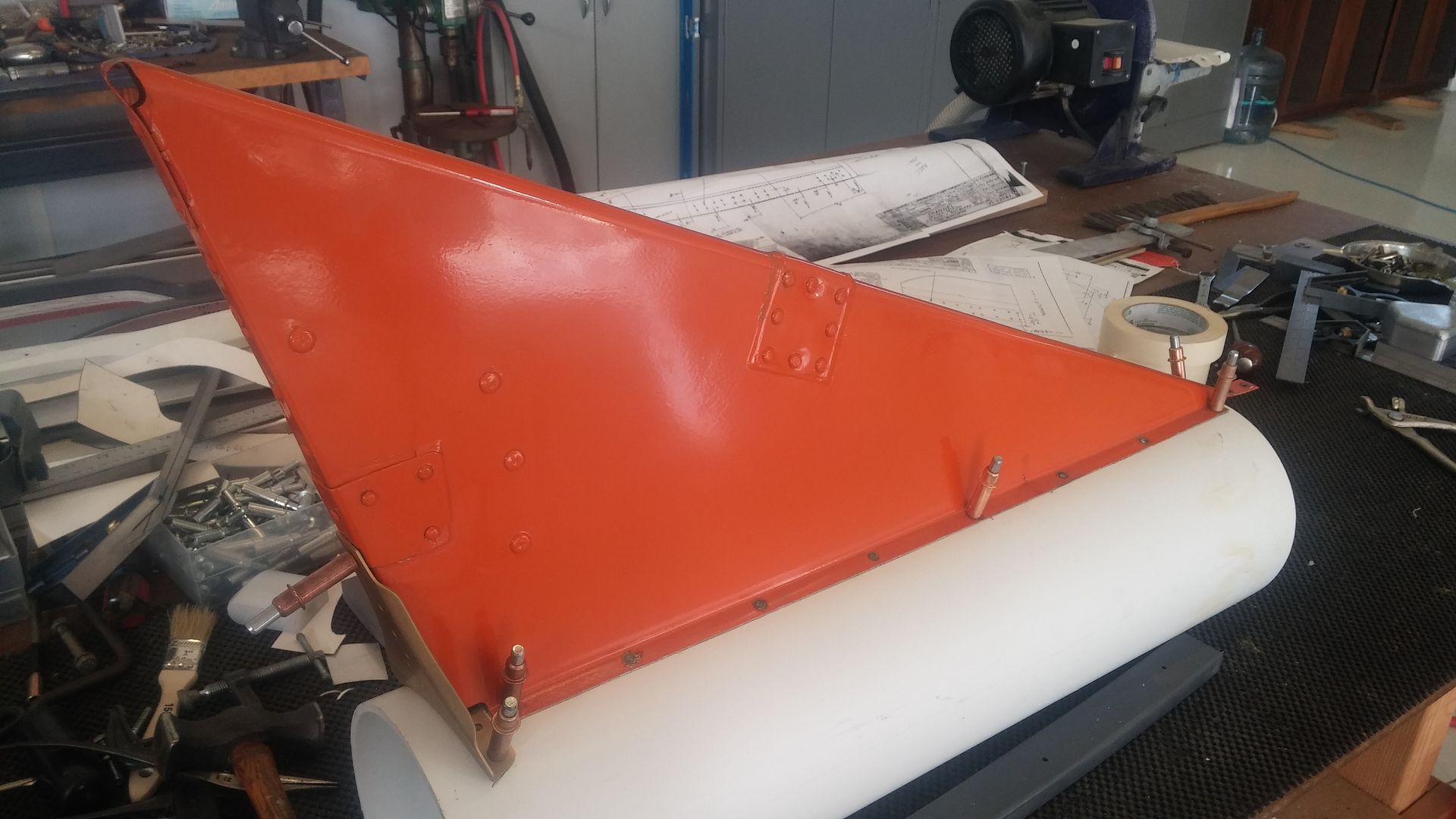
This is the rear mount bracket that has been soda blasted to remove the paint and then, after inspection, re-alodined.
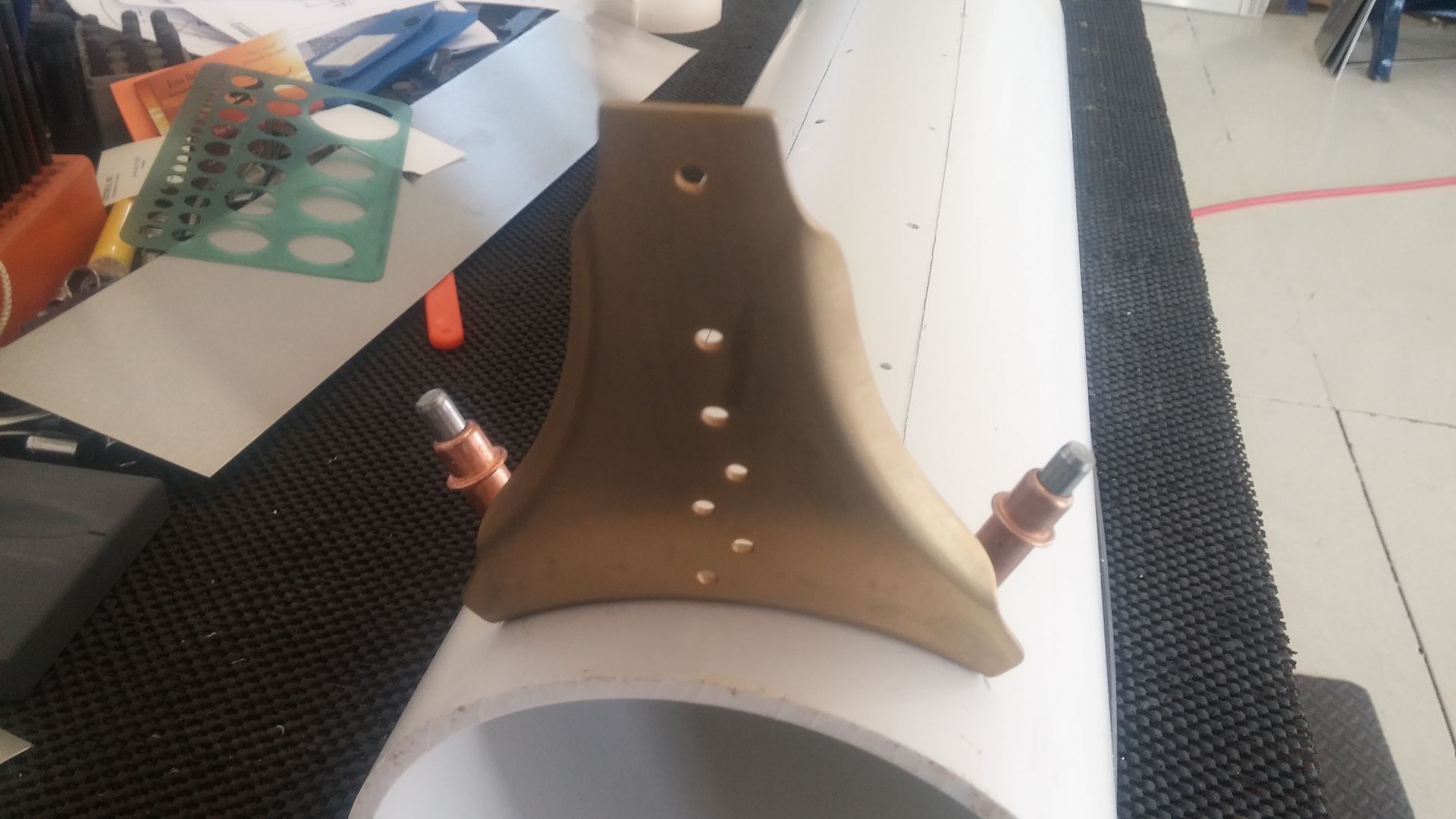
The new one alodined and complete, .020" 2024-T3.
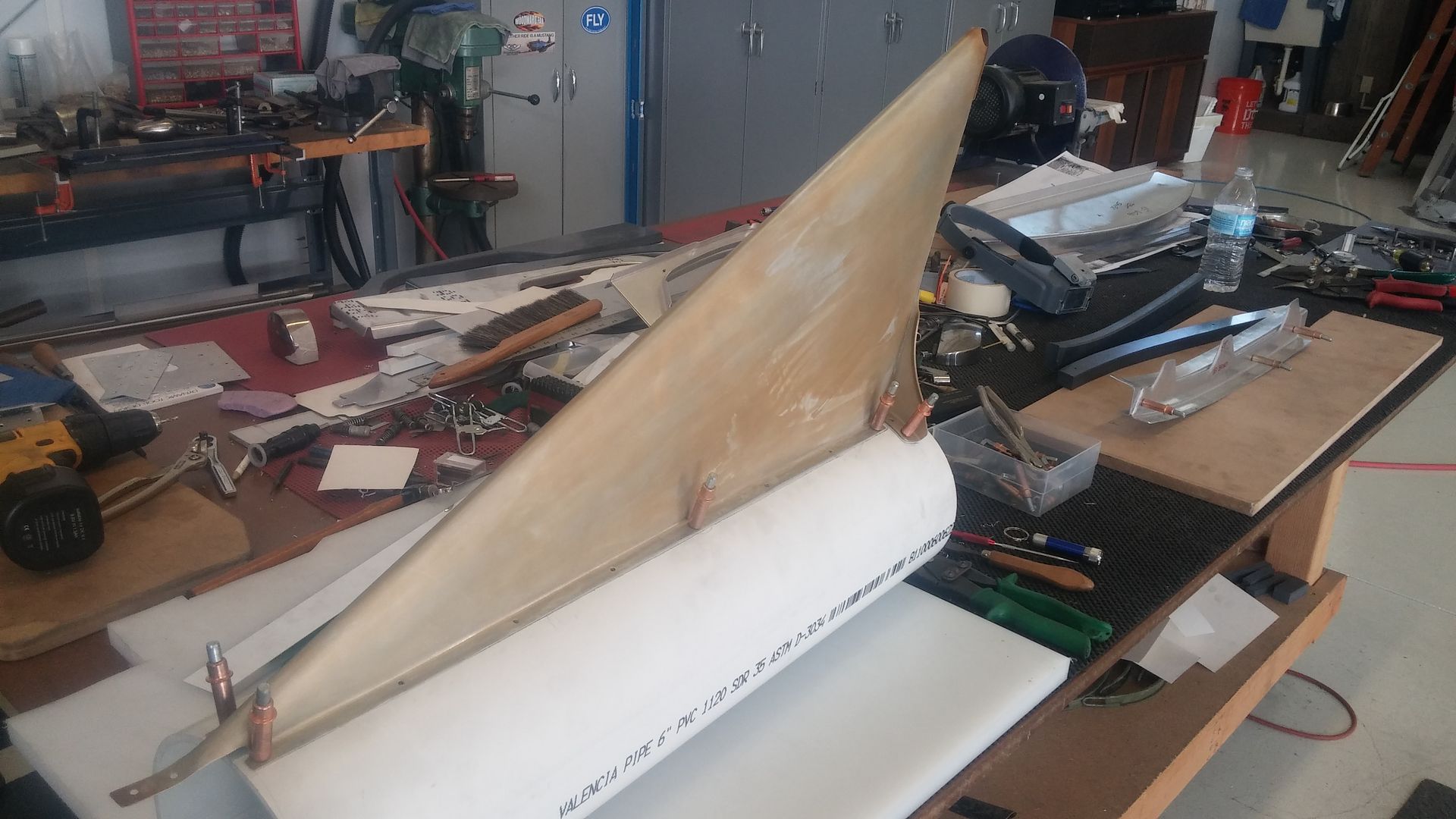
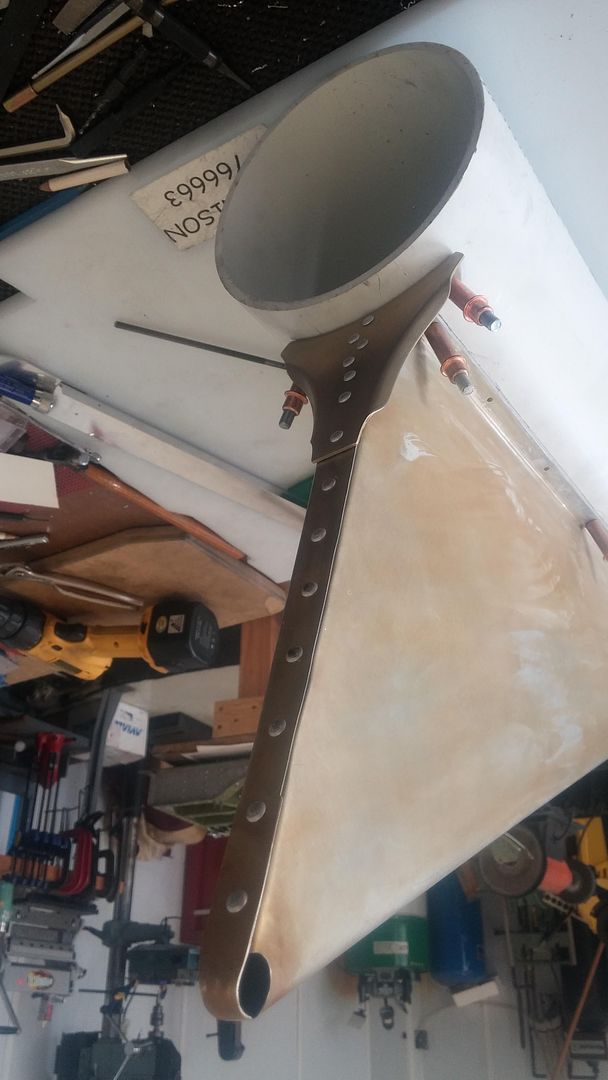
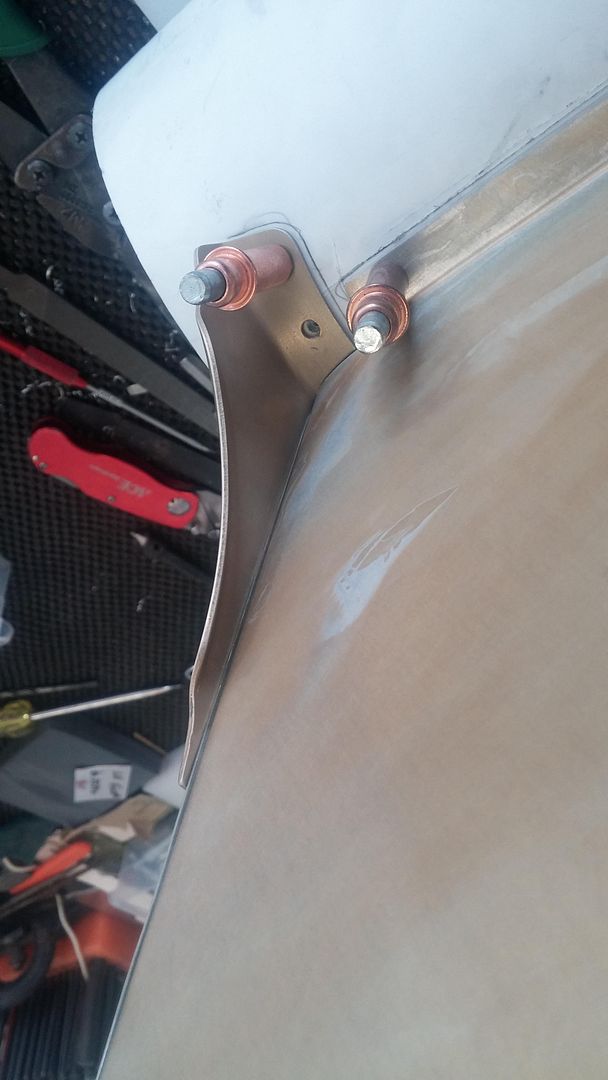
Patterns were made from stranded tape and masking tape for the first FSP. Contour was not important so I used masking tape for extra material. From that, I refined the pattern with another new friend, Home Depot resin paper from the paint department and normally used to protect flooring during construction. Heavier than butcher paper but seems to work well.
Sun Aug 17, 2014 6:41 pm
Scott,
When forming, how much extra material do you leave for trim off? What other tools have you had success using for trim off. I would imagine once a part in formed hand shears can be a challenge to use in all cases.
Regarding the videos, whatever you want to post is fine by me. Maybe a tips video of what to look for and things that might not be so obvious.
Thanks,
PC
Sun Aug 17, 2014 7:08 pm
PC, I normally try to leave an 1/8" to 1/4" depending on the part and shape. I almost always use Wiss snips to do the final trim and actually use my set from 40 years ago because they have no serrated edges. Sometimes I can use the Beverly shear. I try to get real close to size with the trim then if it works, a 10" Vixen file followed by a Nicholson single cut and debur from there.
Here is one video I thought I posted previously. The form is aluminum before I discovered PVC.
https://www.youtube.com/watch?v=k9R8RHaZurw
Powered by phpBB © phpBB Group.
phpBB Mobile / SEO by Artodia.