This is the place where the majority of the warbird (aircraft that have survived military service) discussions will take place. Specialized forums may be added in the new future
Thu May 15, 2014 12:11 pm
As far as I'm concerned, that thumb, belongs to a very skilled hand, owned by an individual, kind enough to share his skills and abilities with us.
For that, I offer a huge thumbs up

(lame crappy pun intended)
Andy
Thu May 15, 2014 3:01 pm
This is very interesting. I check this thread very day, to see what you are up to. You make it real, we are very lucky to get to watch your adventures. I think the name of this thread should have been "Isn't Everybody Interested". It isn't everyday you get to see a skilled craftsman at work, and have him tell you the purpose, method, and the logic of his work.
Thu May 15, 2014 10:37 pm
Thanks guys for the kind comments.
Left hand done, right hand next. The form block is radiused on both sides to make both hands.
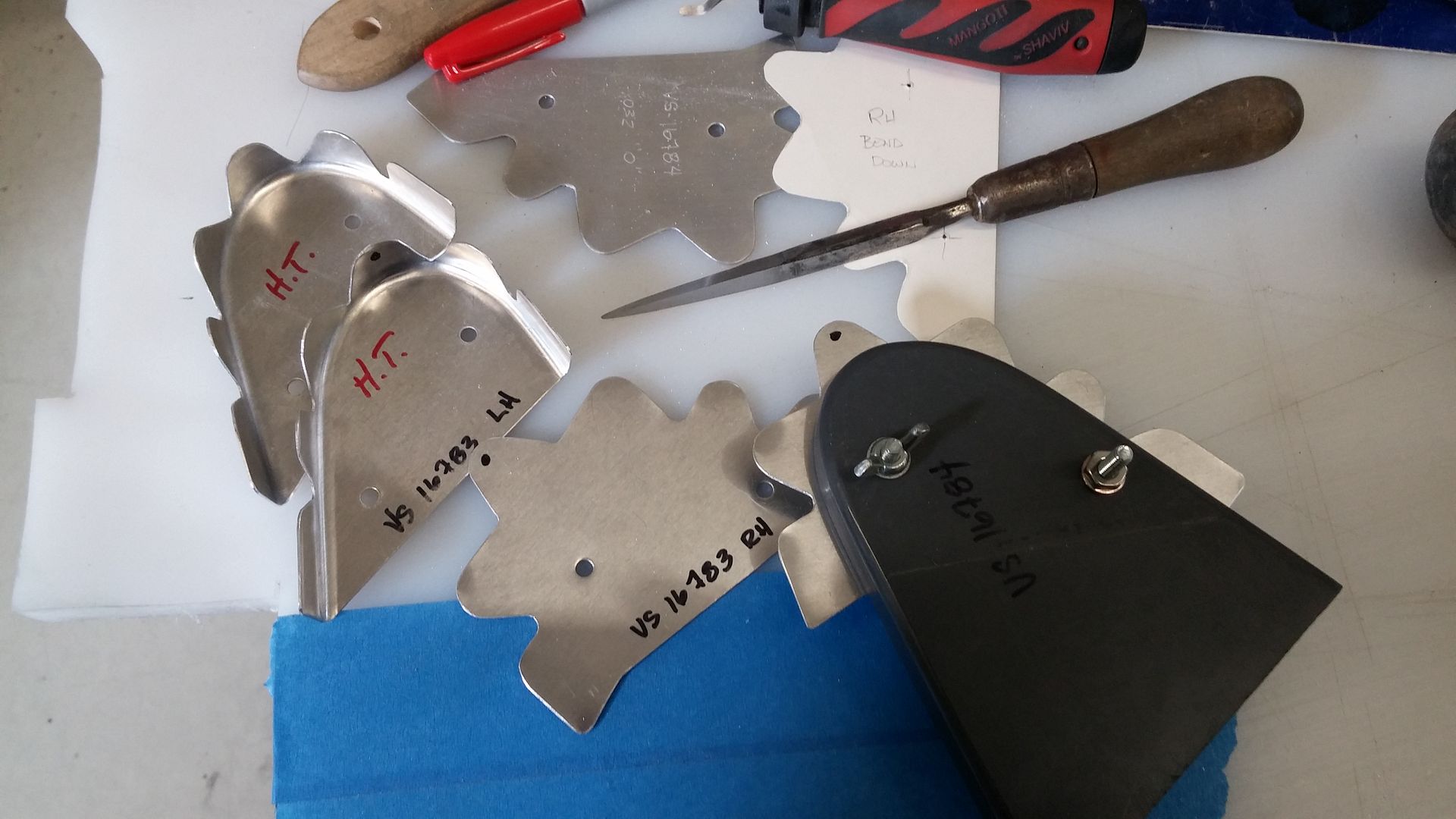
The dot helps my old brain remember which way to fold the ears.
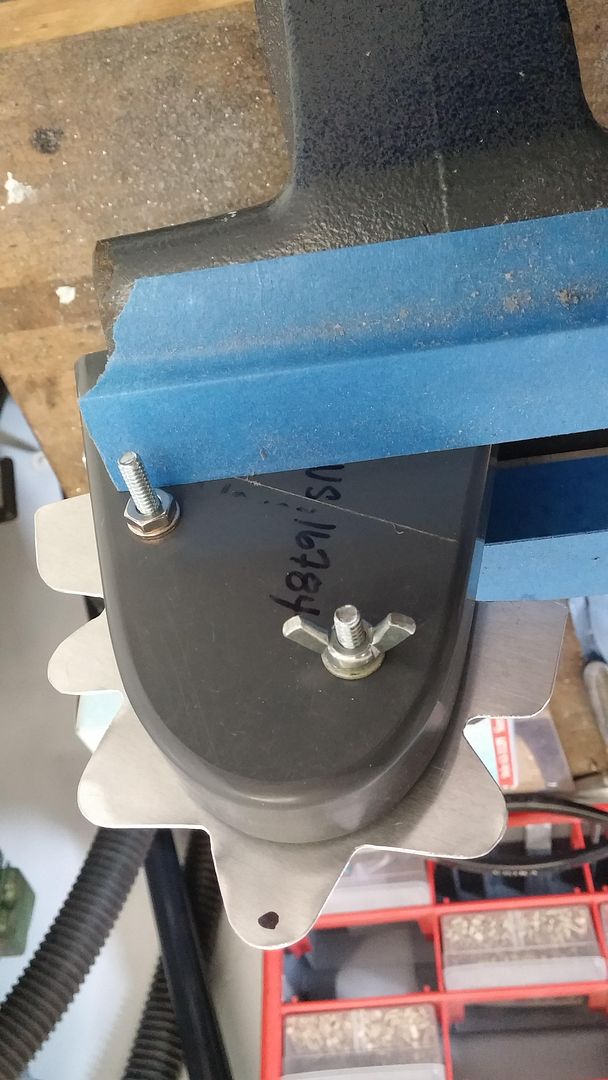
So, what was involved to make these six ribs? The ones shown in the upper left were covered earlier in this thread but these three attach to the leading edge skin.
Mon May 19, 2014 7:39 pm
Today, we started the leading edge. Left hand side.
Now, I found this official Corsair forming tool that made the job fairly easy.
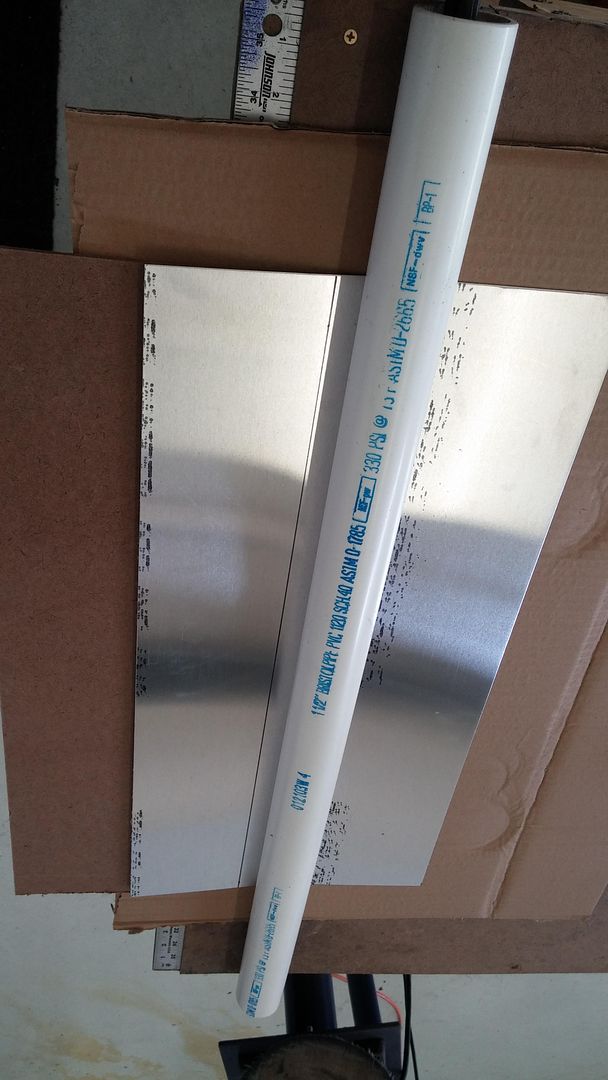
I used cardboard for padding and protection. Clamped the PVC at both ends. Did the fold using a piece of masonite to equalize the folding pressure and get a flat plane fold.
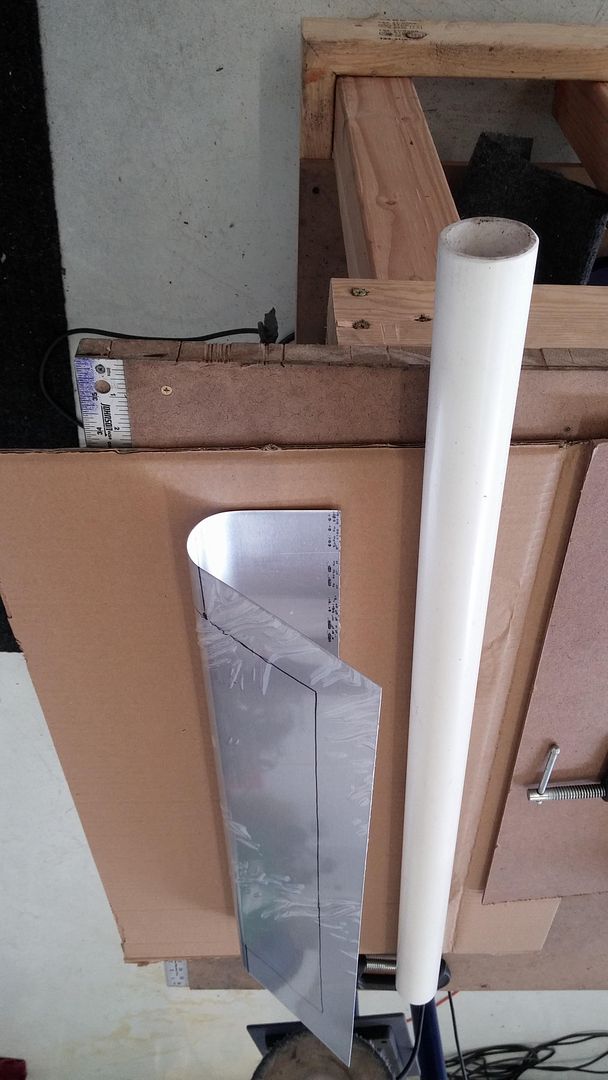
Next came the trimming.
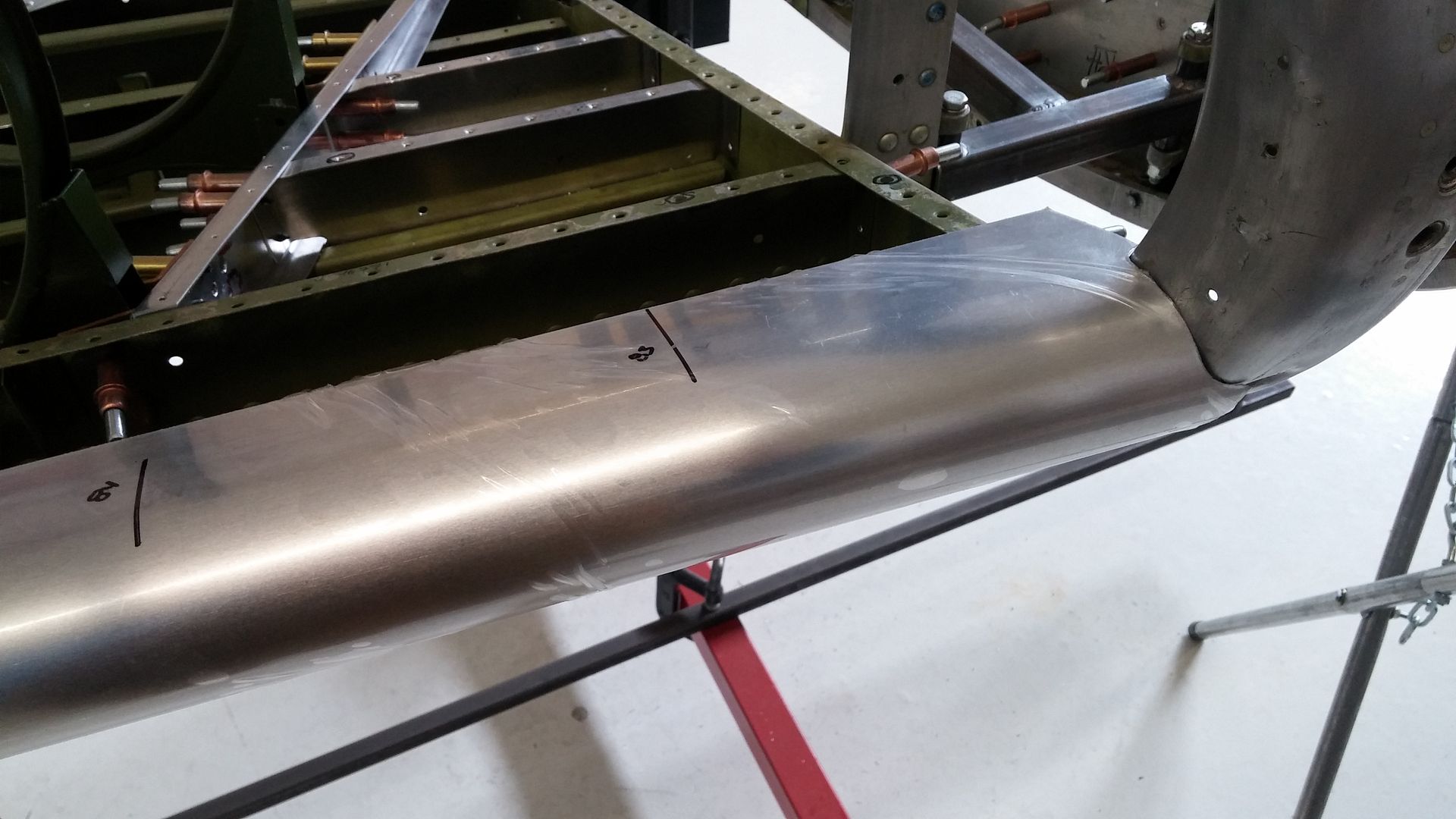
To fit our plane's contour, I needed the help of the outboard fairing. Note that the racers cut this in half and that will be another project later on. The alodined piece is a reinforcing rib to match the edges of the two skins.
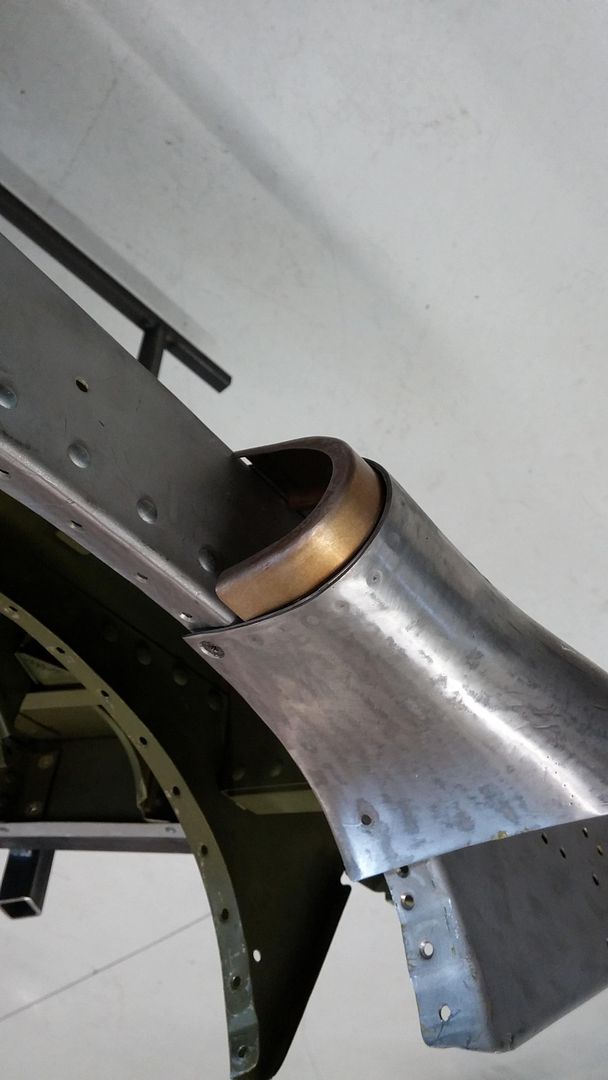
The skin also gets a simple doubler over the rib.
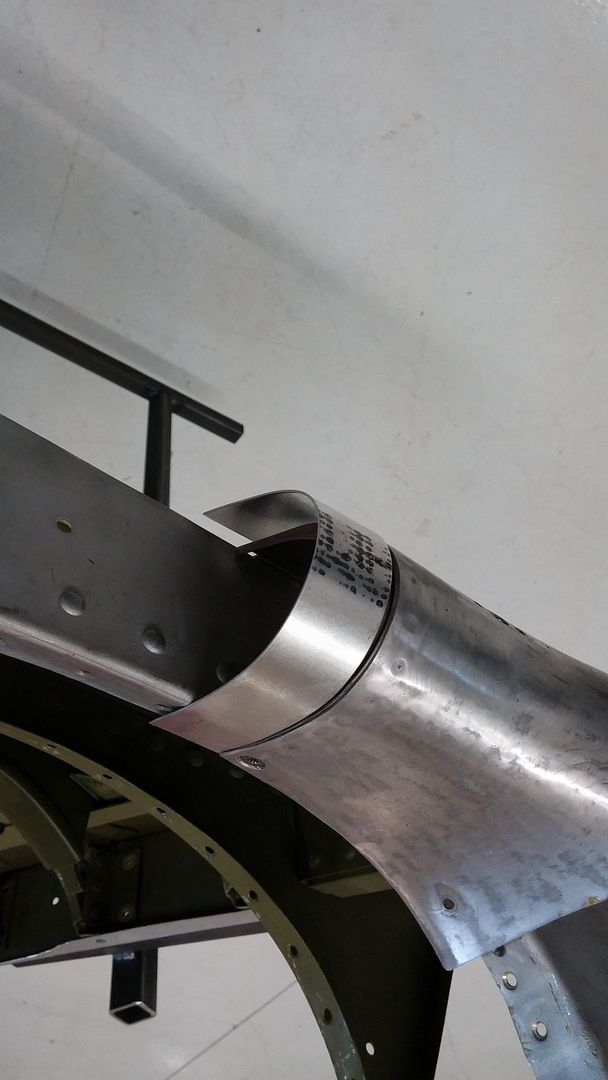
This side starting to fit well. Notice the slight form at the cooler opening.
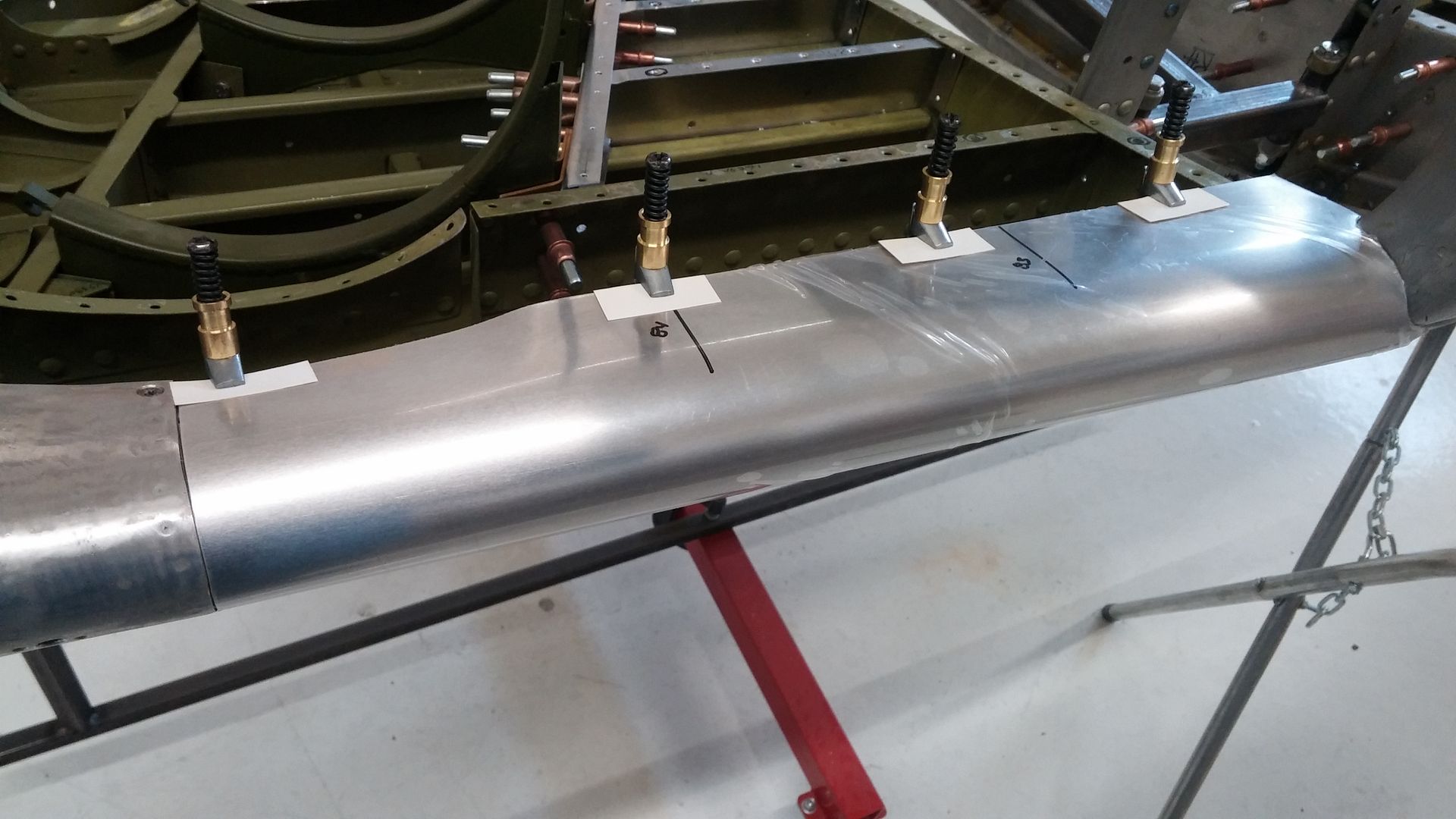
Probably too tight a fit but if it works great, if we need to open it up some later.
Wed May 21, 2014 7:37 pm
A day of FSP making. The lower sections of this project have to be made from scratch complete so I thought I'd start with the skin patterns as I work deeper into the structure. I use strapping tape and do 5 to 6 layers in different directions and try to not overlap seams. When removed, they hold the shape amazingly well.
These are the individual skin sections required less the leading edge which I will make next.
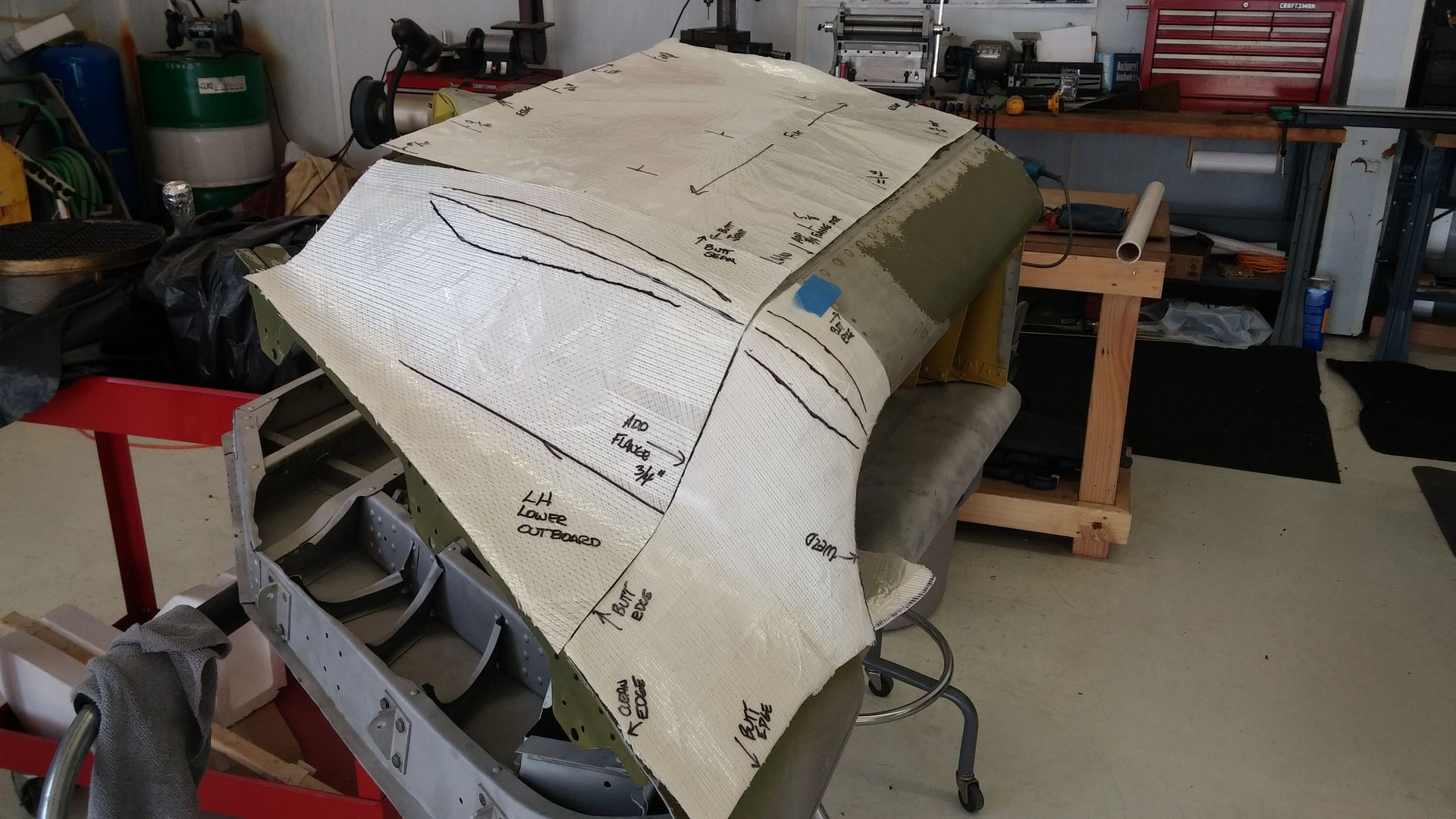
This actually makes the inside of the fairing, if you flip the FSP over in this picture. The black line will be the weld seam.
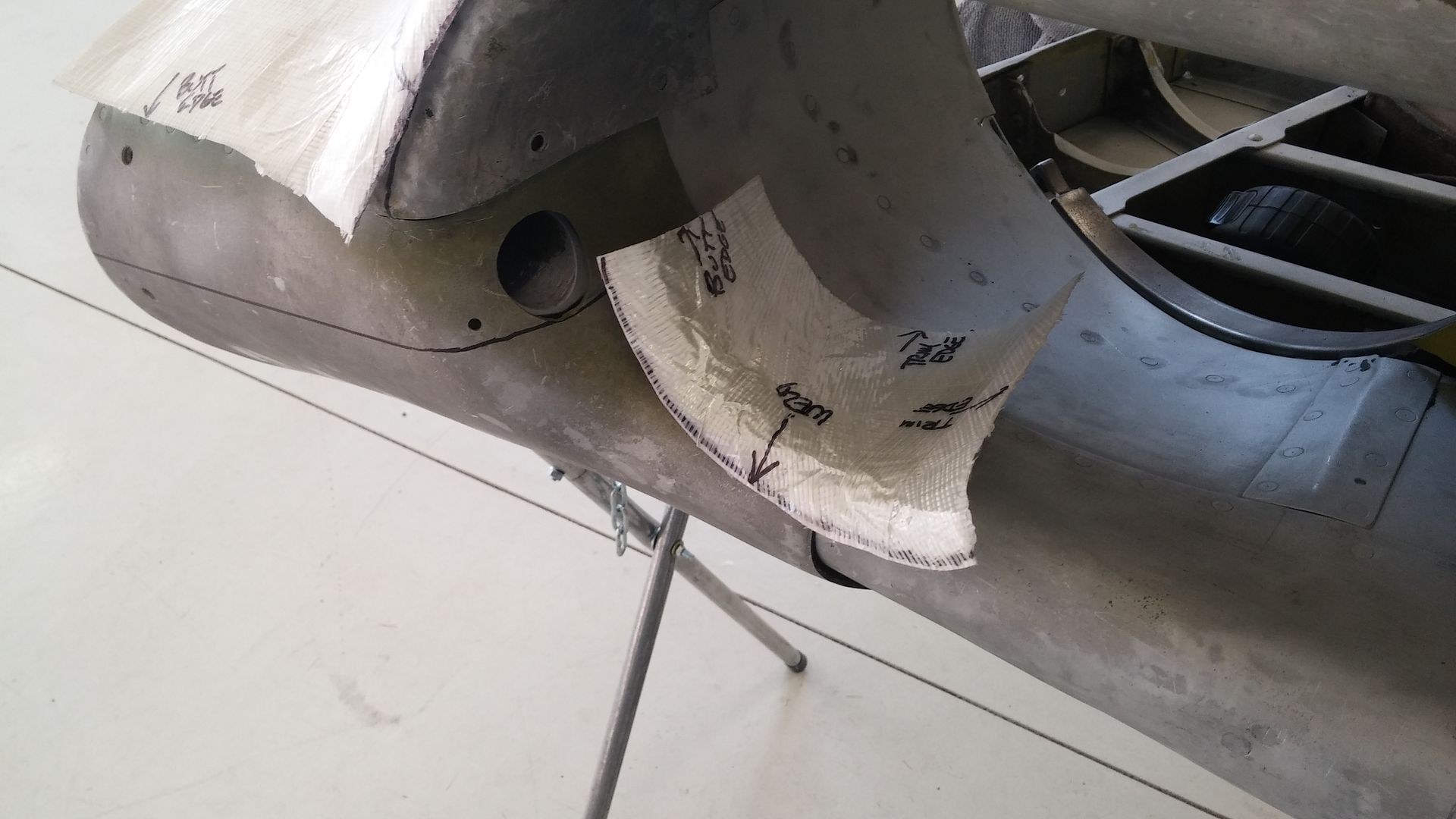
On the upper half, the racers cut this fairing down. I will probably just make the missing piece rather than recreate the whole thing new.
Sat May 24, 2014 7:15 pm
Repairing the inlet fairing. The race mod cut the opening way down and made new skins for the leading edge and lower skins. Rather than completely remaking, I am making the missing part and will rivet it back on. The lowers will need to be made new complete. Remember in the pictures, the sections are upside down in my fixture.
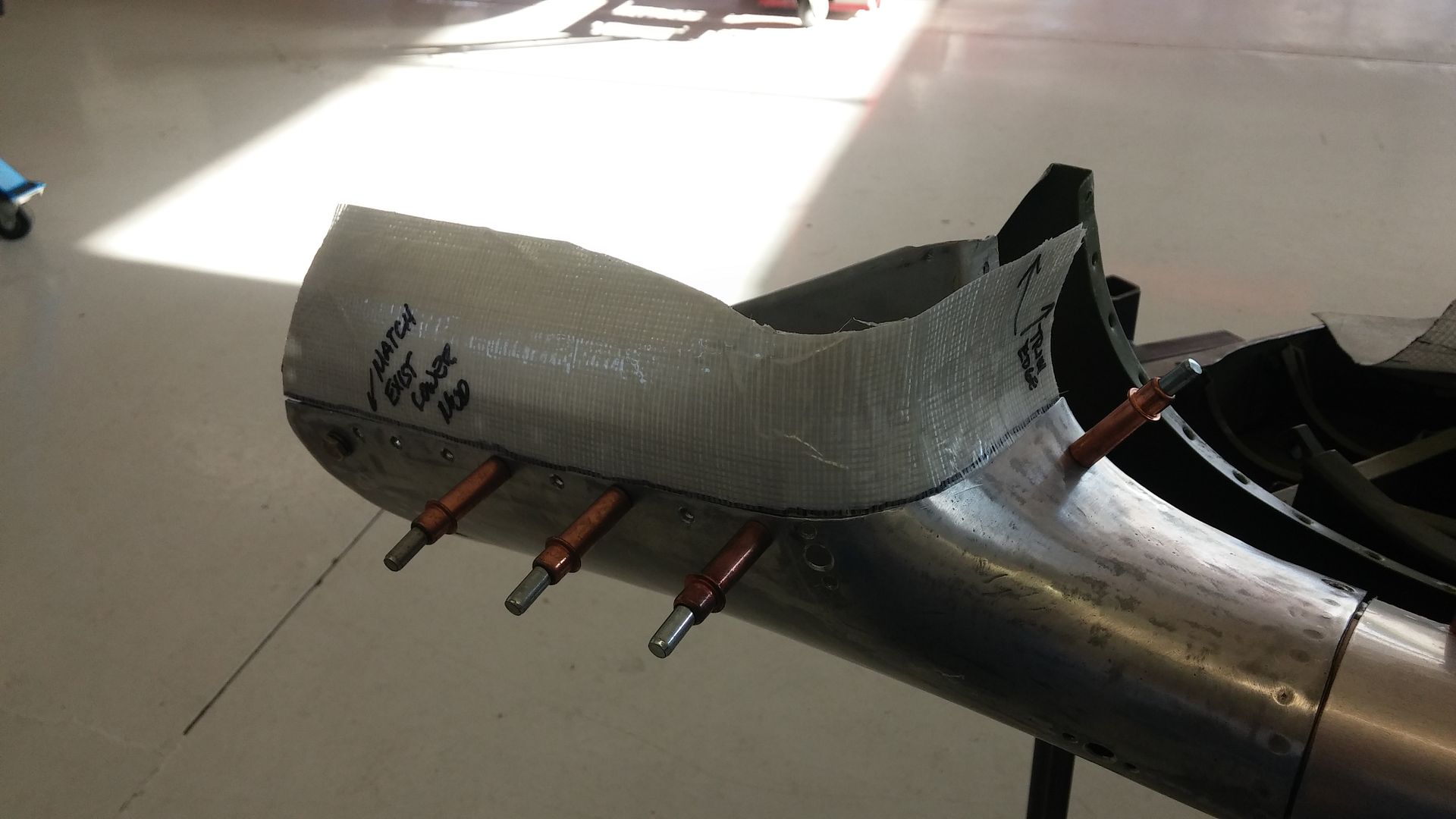
Needs some trimming and tweeking yet
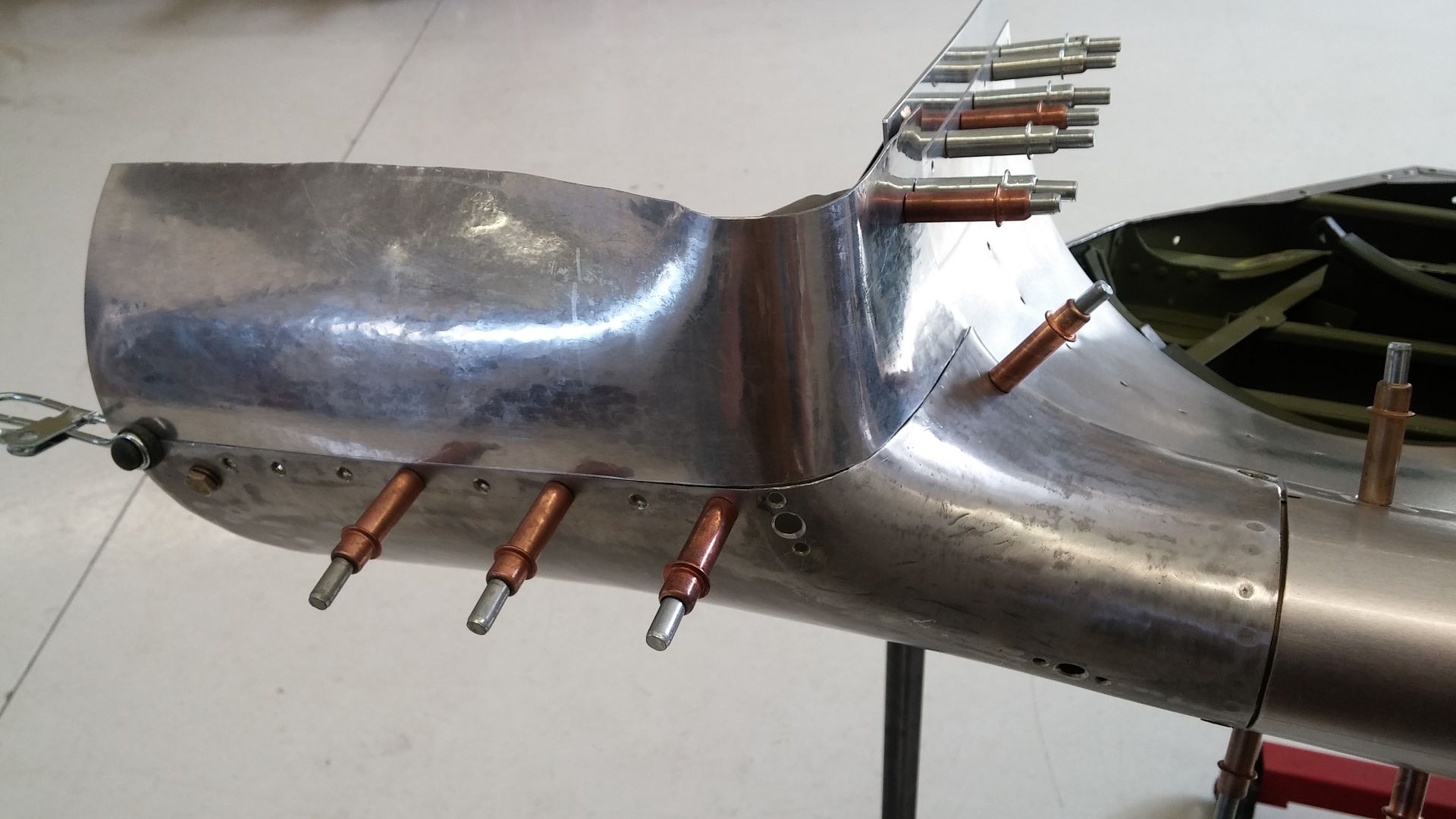
Another view
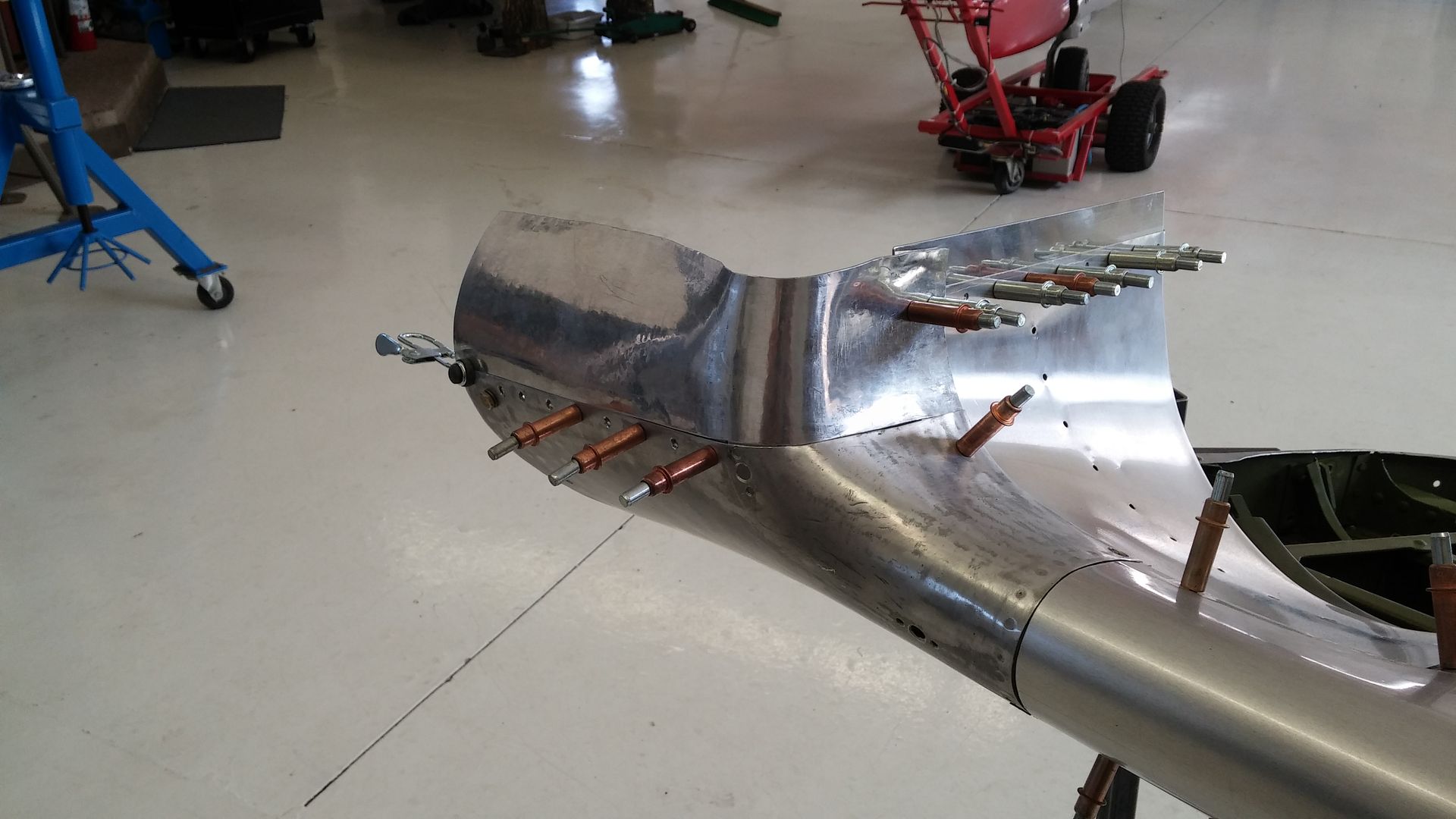
Modified opening
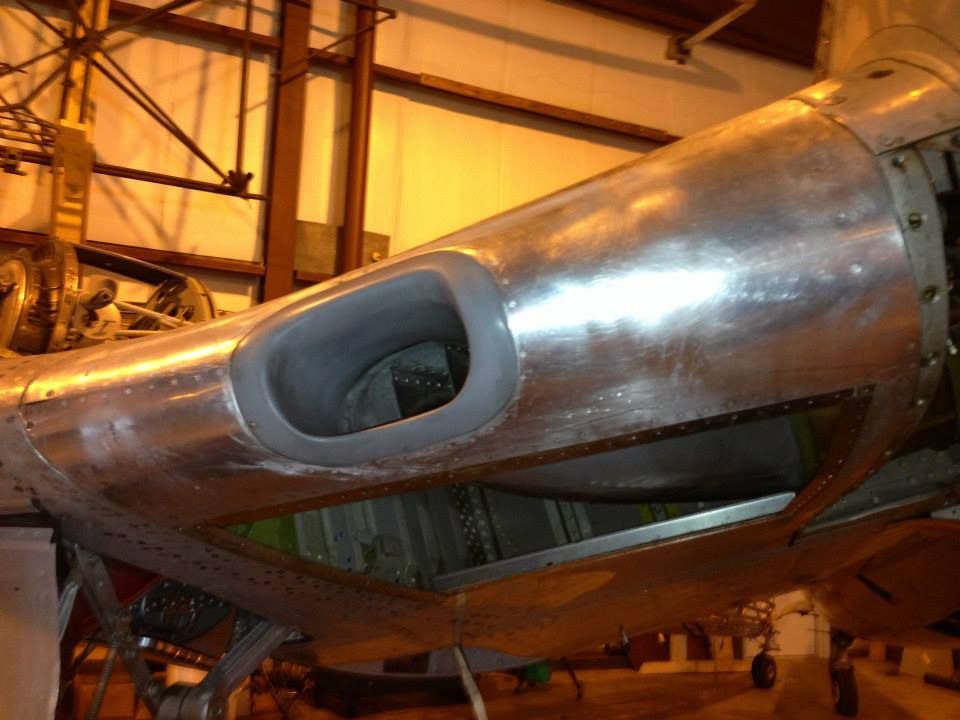
Stock opening
Thu May 29, 2014 4:05 pm
Could you make me another one while you are at it?
Absolutely beautiful metal work!
I am hoping it will still whistle with that modified wing inlet.
SPANNER
Thu May 29, 2014 10:23 pm
Thanks Spanner but I'm going from the modified returning to stock. Should include the whistle automatically.
Fri May 30, 2014 8:05 pm
These lower sections do not exist for our bird and will need to be recreated in total. So today I started making some contour gauges with 1/16" x 1/2" aluminum and used the shrinker/stretcher. Then I started working on the lower LH skin. The FSP's made and talked about a couple days ago are really good gauges for shape.
A couple of the gauges
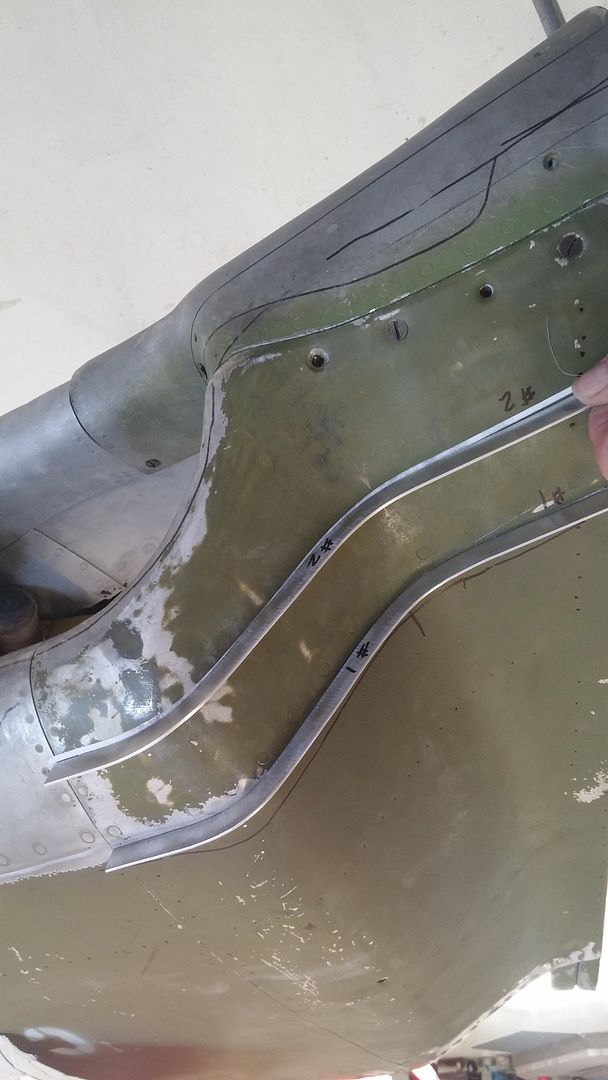
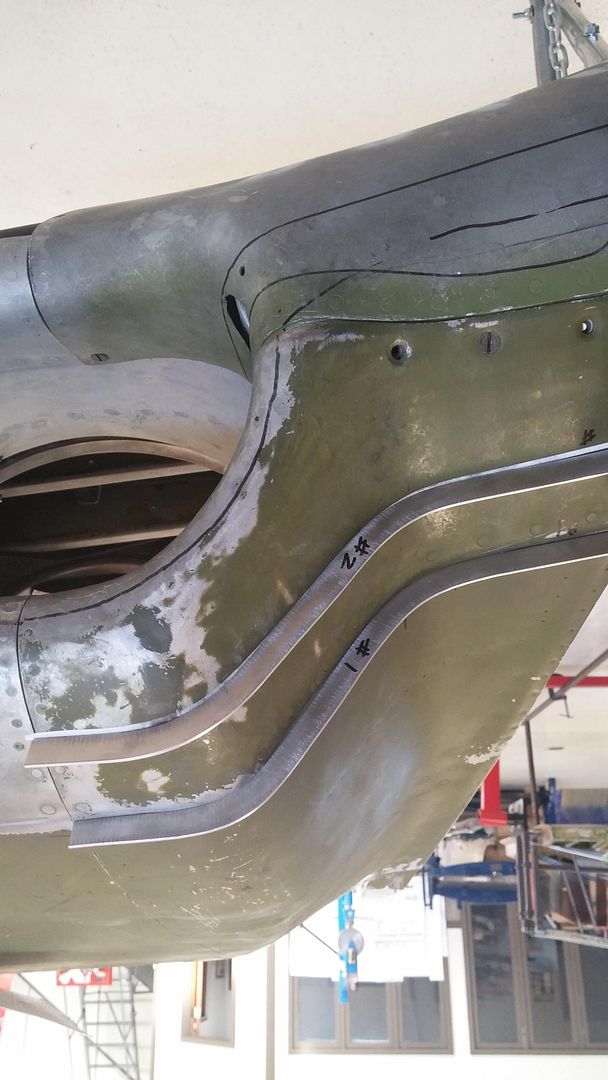
Initial skin form.
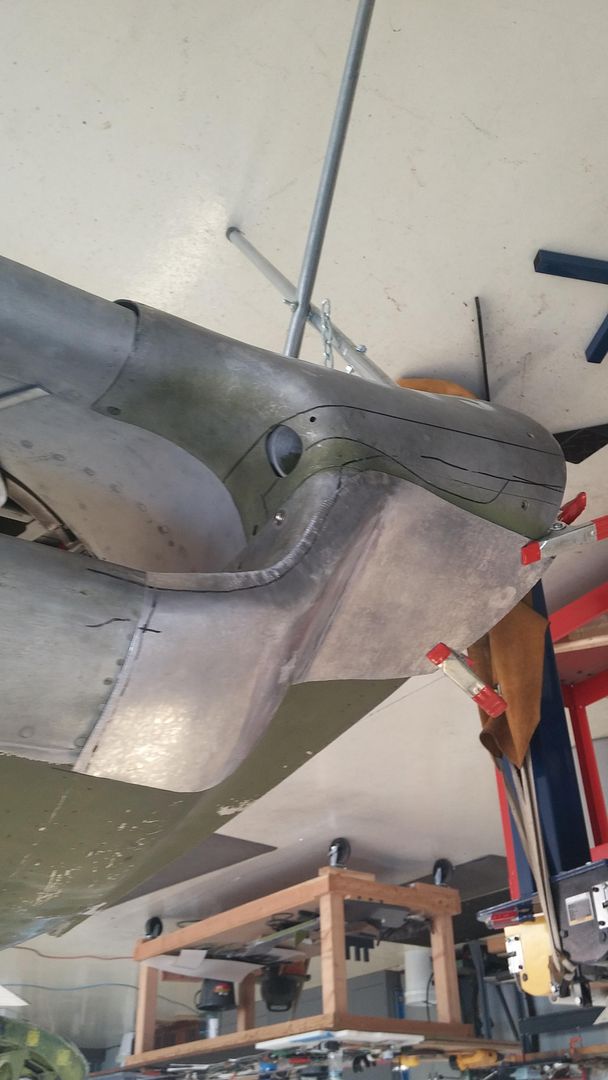
Close but more work needed to be correct. I have a new idea and will share it if successful but could really help...
Wed Jun 04, 2014 9:33 pm
It would be great if the original shape could be laser scanned, imported into a CAD/CAM package, and have a male blank machined out of MDF. That would make the forming a bit faster. Your method obviously works spot on so I could only offer advice on speeding up your perfection.
Thu Jun 05, 2014 10:44 pm
My and my shrinker did some work...
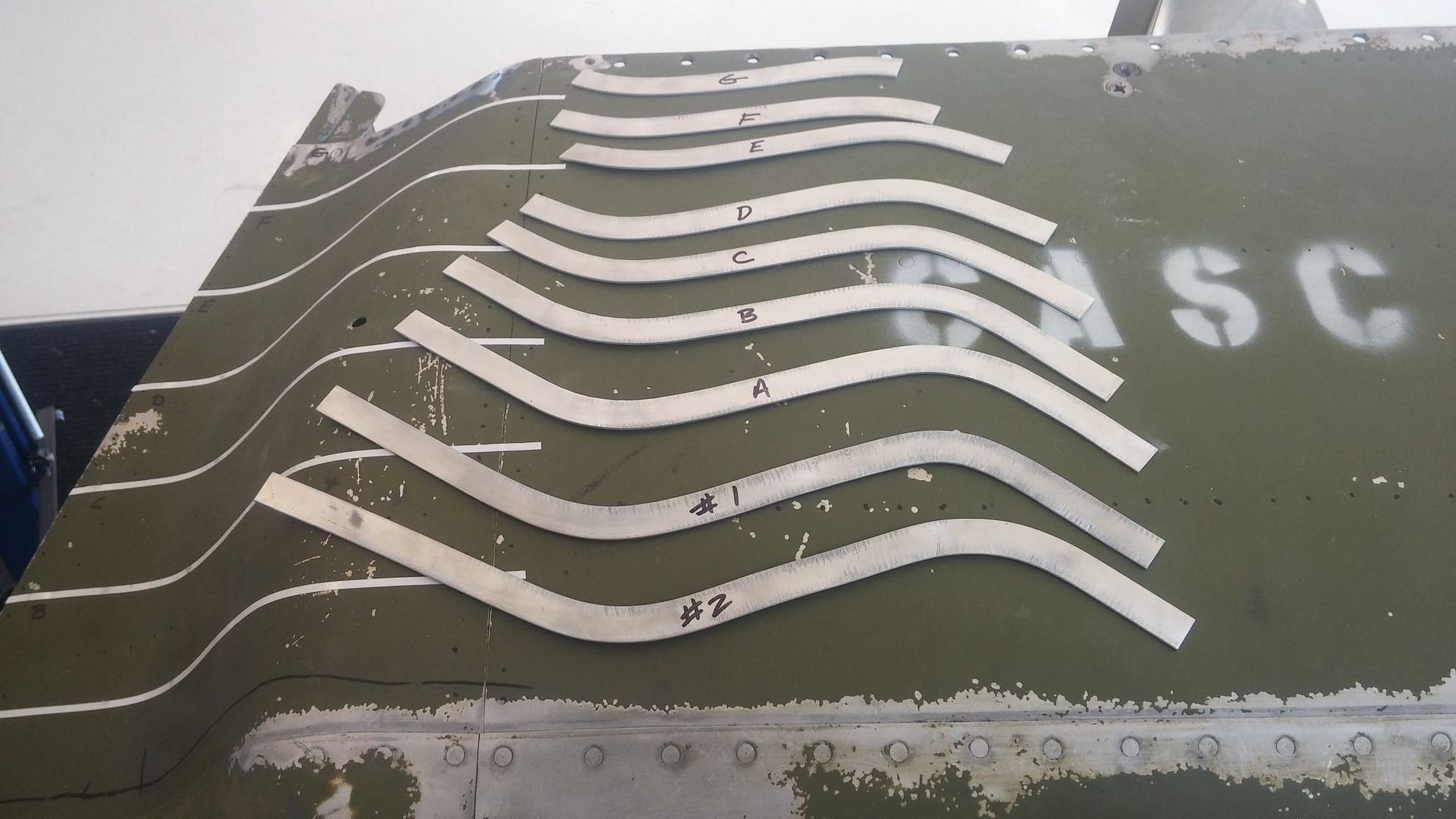
Then made a trim piece for a 1947 Lincoln convertible.
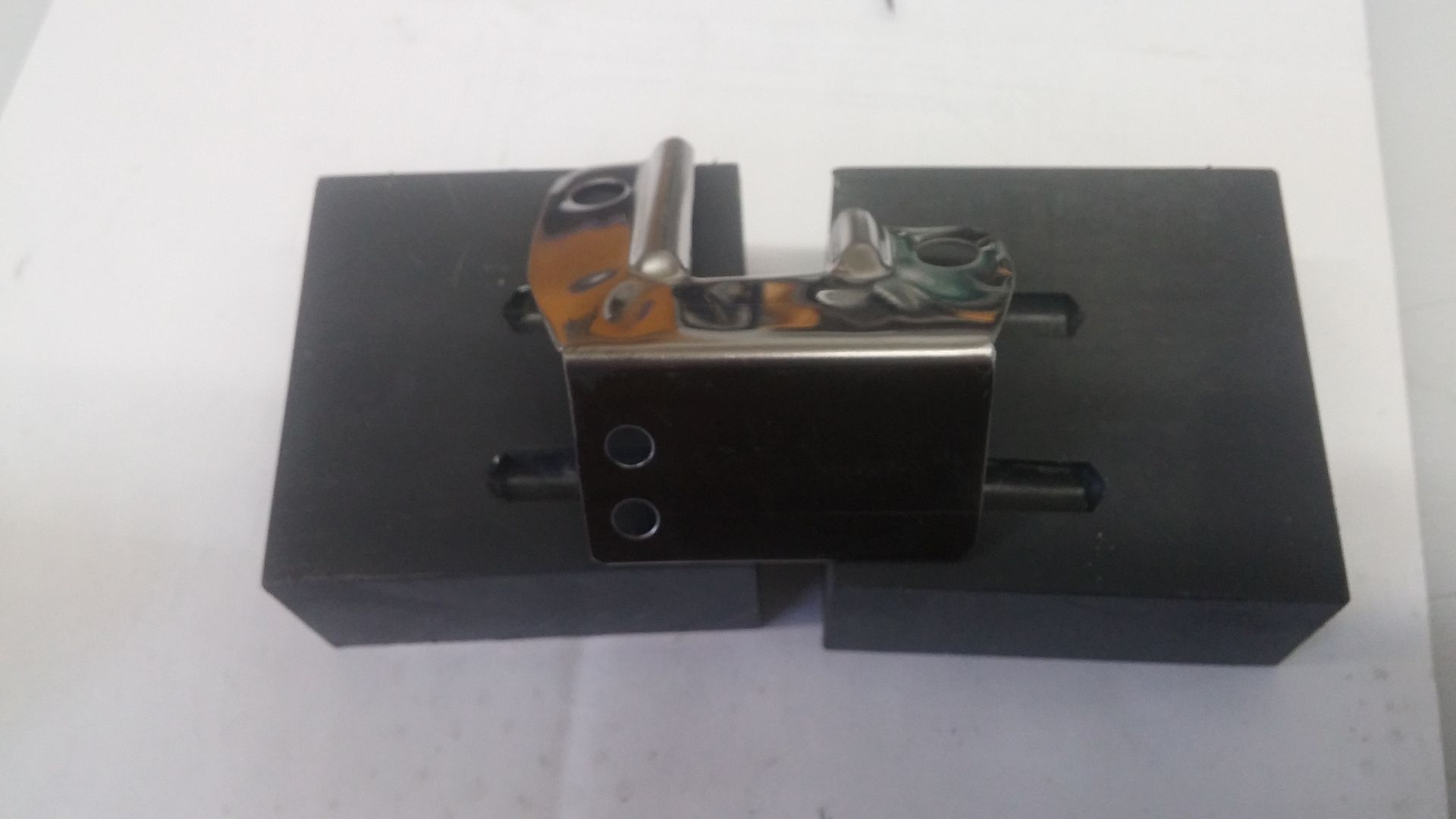
[/url]
Thu Jun 05, 2014 10:58 pm
Stainless steel? I hate bending that stuff. There is an acre of it on my 57 Chevy.
Thu Jun 05, 2014 11:08 pm
Yup but only .016". Easy to work. Only 10 of these Lincolns remain. Guy had been looking for this part for a year.
Fri Jun 06, 2014 12:26 am
That's pretty thin! I bet he was happy to find a way to get the part. And a mighty fine one too. What polish rouge do you use?
Fri Jun 06, 2014 7:36 pm
AURktman wrote:That's pretty thin! I bet he was happy to find a way to get the part. And a mighty fine one too. What polish rouge do you use?
Yeah, thought he was going to cry. I think he is rather emotionally involved in his car. Cool to make someone that happy. Polish is as purchased at my local hobby shop.
So, today, finished up the contour templates for the left side and reversed, should be good for the right side. Then moved on to start the design for a solid assembly fixture for the lower assembly.
Powered by phpBB © phpBB Group.
phpBB Mobile / SEO by Artodia.