One of the ongoing maintenance issues with a project like this is replacing pretty much every O-ring and rubber seal throughout the aircraft and its systems. We are getting to them slow but sure but some demand to be put at the top of the list. We have had a weeping shaft seal on the flap cylinder for a little while and it was time to fix it. The flap cylinder on the PV-1 and PV-2 are mounted in a box near the rear spar in the center of the fuselage. You have to step up on to this box which also is the aft support for a floor structure between that and the main spar or in Navy/Lockheed terms; the main beam.
A cover is removed which gives access to the cylinder and the pulleys that make up a part of the Fowler Flap control system. The Fowler Flap system is not your average flap system and it was quite advanced for its time. I'm shooting from the hip here so beware: Robert Fowler invented this flap system that would allow a dramatic change in the airfoil of the wing. Instead of a simple hinged flap that makes up the trailing edge or a split trailing edge his system would move a separate airfoil on tracks back and down thus significantly changing the airfoil or shape of the wing. His system was a vast improvement and was real efficient.
How the Fowler flap system operated, especially in the early days, involved a lot of cables, pulleys and tracks and trolleys. The Fowler flap system is still in use on pretty much every airliner and many other aircraft built today. from what I understand Mr. Fowler invented the system back in WWII and donated the technology to the aircraft industry for the war effort. He was supposed to receive royalties after the war was over but never did. I heard he died a poor man. Once again it is hearsay from a friend of the Fowler family so take it for what that is worth.
Since the 2014 airshow season was fast approaching Ricky took on the leaky flap problem and he started in January. He determined that we would have to de-rig the flap cables so the cylinder could be removed from the cylinder box. On the Fowler system one main cable will go into a tube and attach to a disc and three more cables will attach to the other side of that disc. Those individual cables head off and multiply themselves into several more cables. Needless to say it is quite the array cables heading off all over the place two of each going to each trolley and there are five trolleys/tracks per flap. Adjusting one cable changes tension and thus rigging on all of the others and can cause uneven flap tracking which can cause rare and important parts to tweak, bend or otherwise be real unhappy.
This is a shot from the maintenance manual showing the flap system and its cables and pulley compliment:
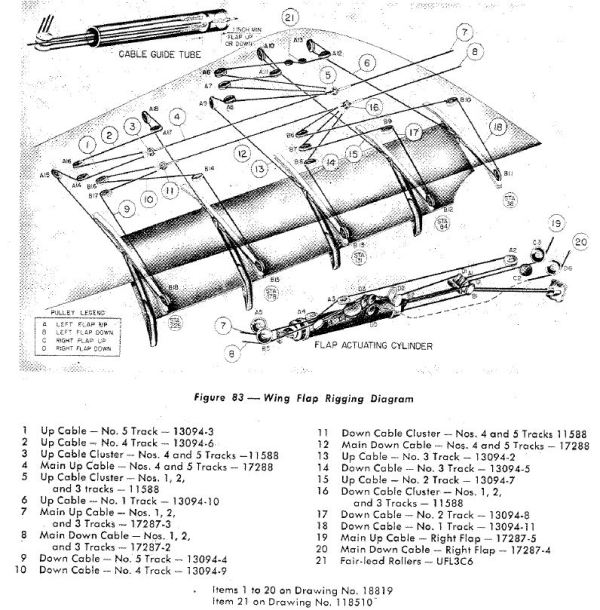
Here is Robin helping out Ricky by removing one of several tubes that cover the one cable into three assemblies. This tube keeps the disc and cables in place and lets it move smoothly without snagging on surrounding structure or other cables.
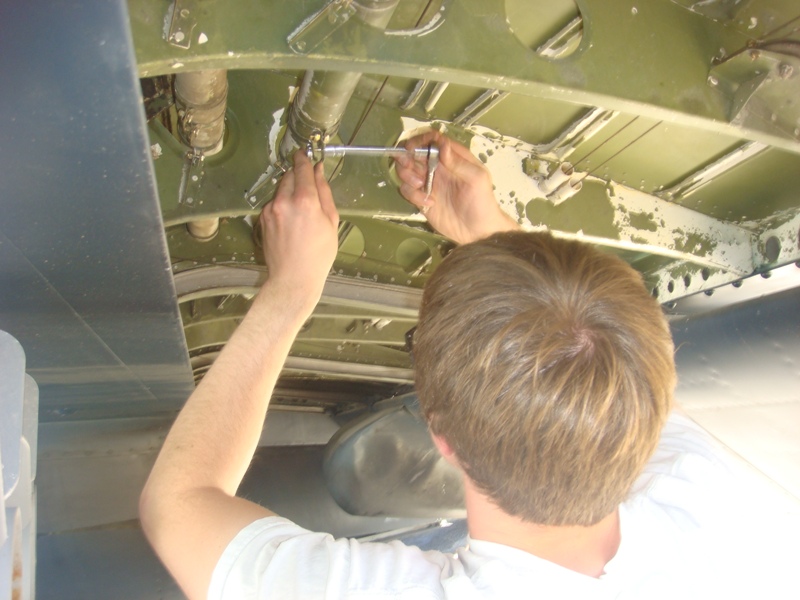
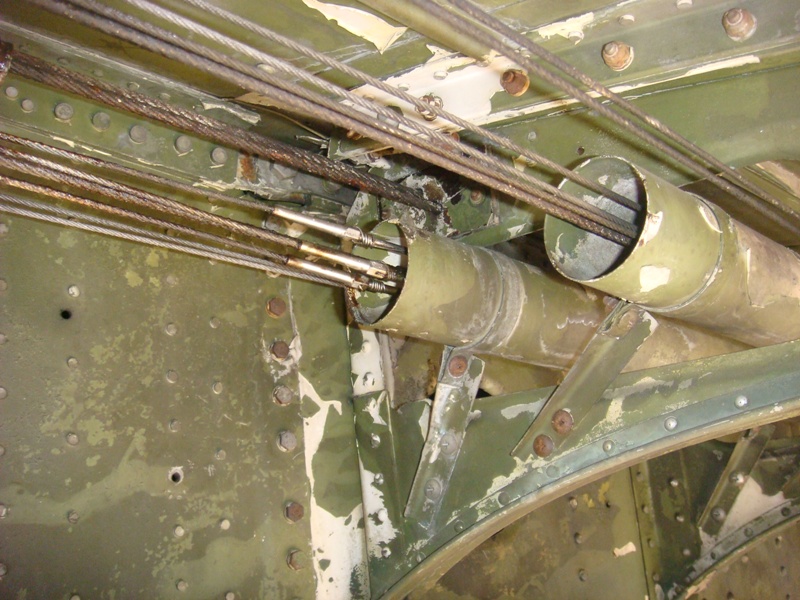
Removing the tubes allows the main cables to be disconnected thus relieving the tension so they can be removed from the flap cylinder and its pulley/block and tackle mechanism.
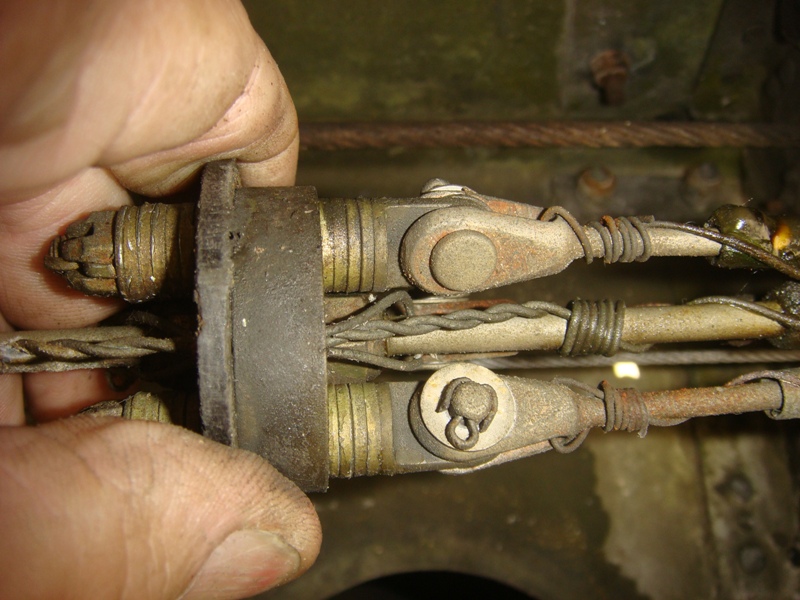
Cousin Mike even came out and helped Ricky with this project. Thanks Cousin Mike! In this shot you can see one of the five flap tracks on each side of the aircraft and the cables that run to the flap trucks or trolleys. There is one up and one down cable per truck. The bumps or protruding fairings on the trailing edge of the wing cover up the aft end of the flap tracks. The same is true today on those big fairings on the wings of airliners.
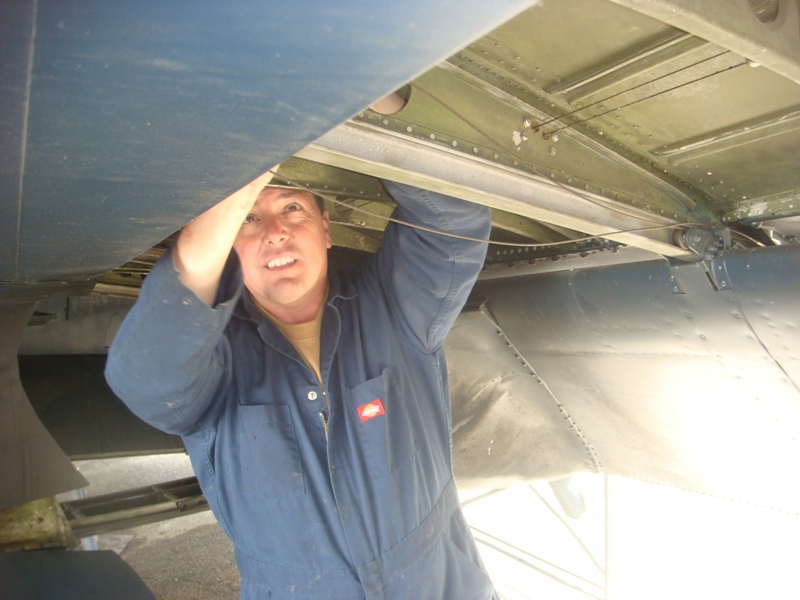
With Robin looking on Ricky is removing the cylinder in less than ideal conditions. Access is limited and a second set of hands is often needed from the bomb bay side.

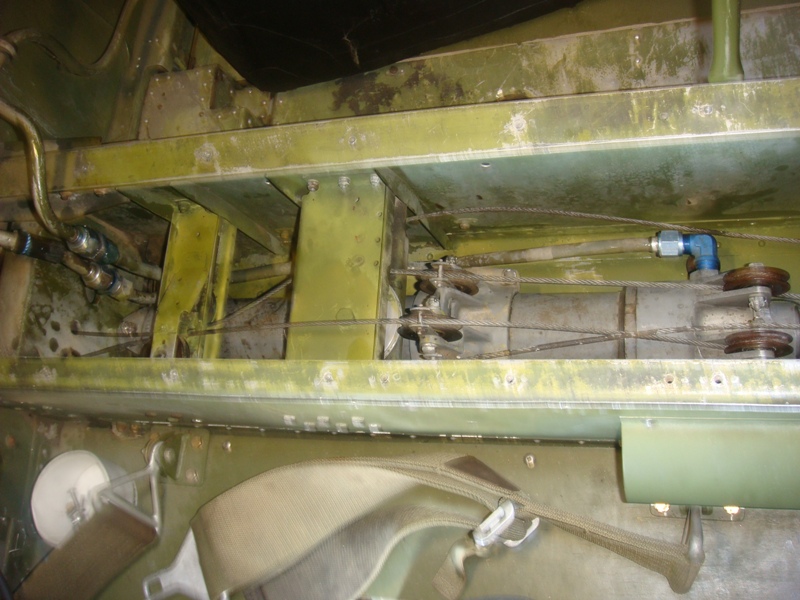
Here is Ricky with the flap cylinder in question. It took a long time just to get to this point.
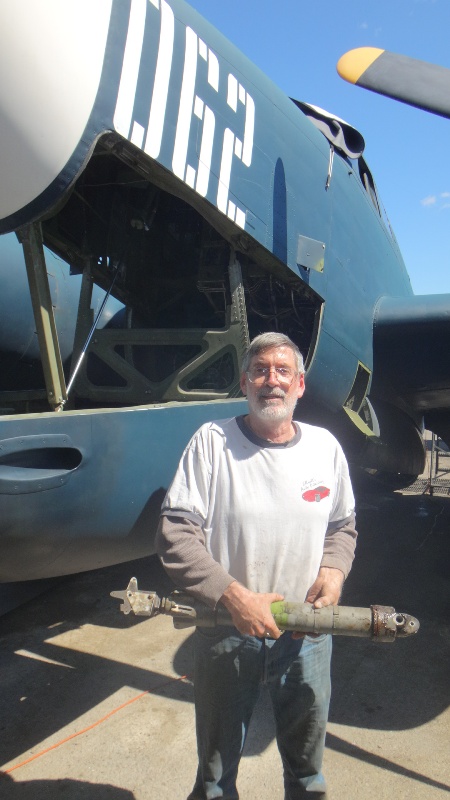
After the cylinder is removed for rework the well and box area is cleaned and prepped. Robin took on this job.
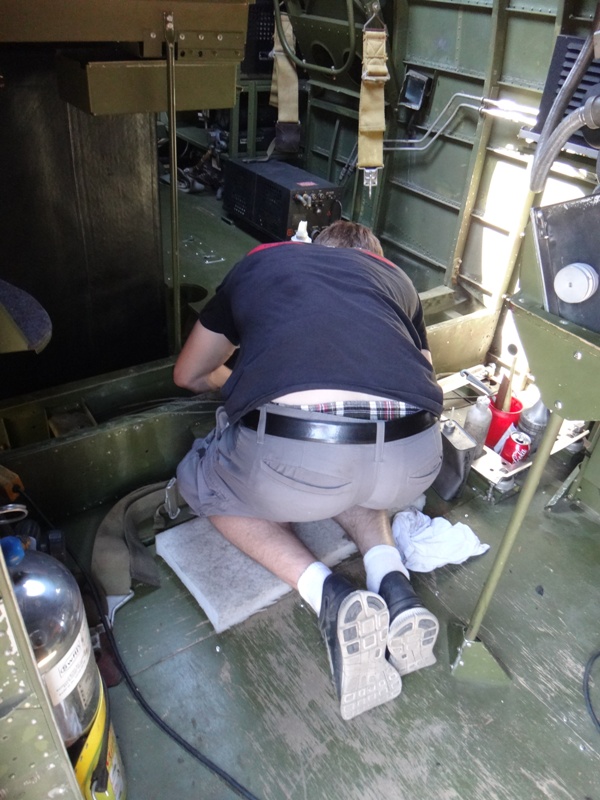
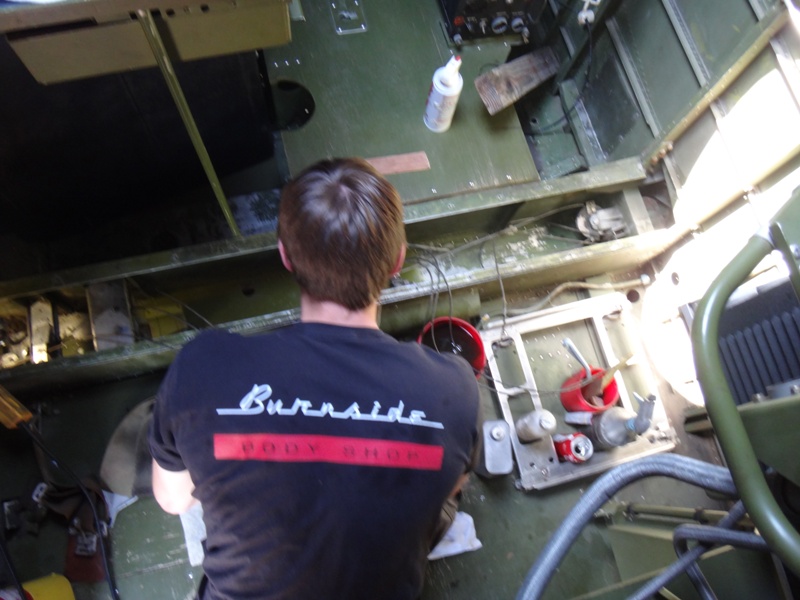
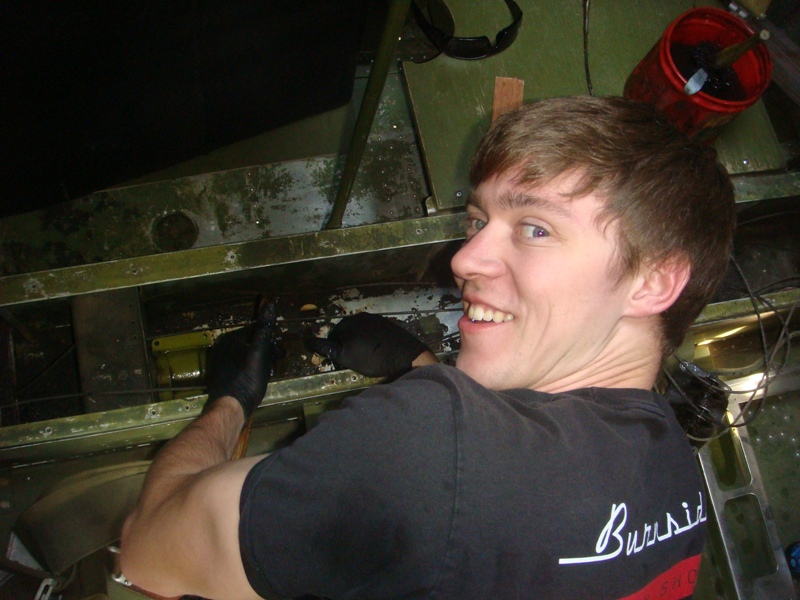
Some interesting graffiti shows up around 062 when accesing the flap pulleys. Connie Hirth from Hirth Air Tankers name appeared for about the 5th time as did some factory comments and noted from Lockheed Burbank
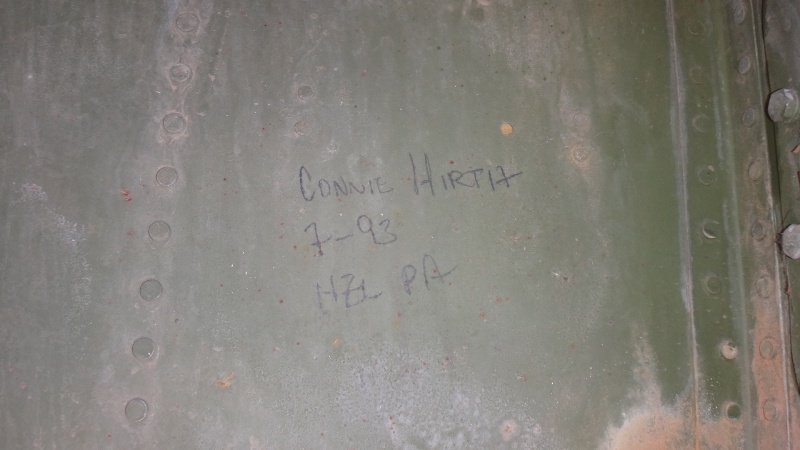
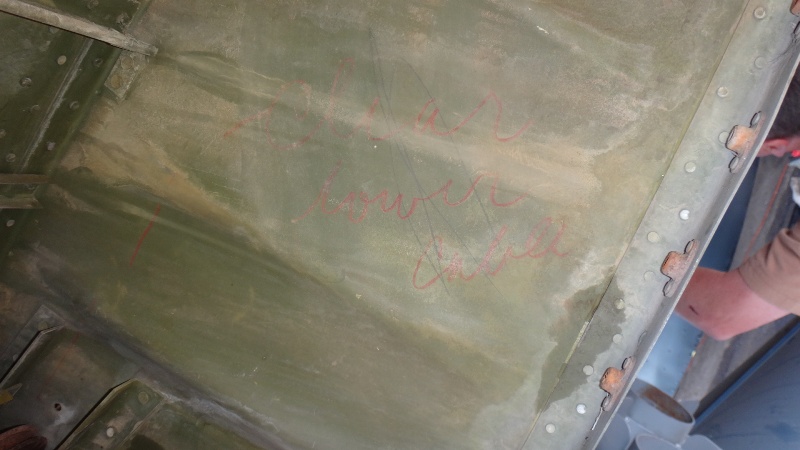
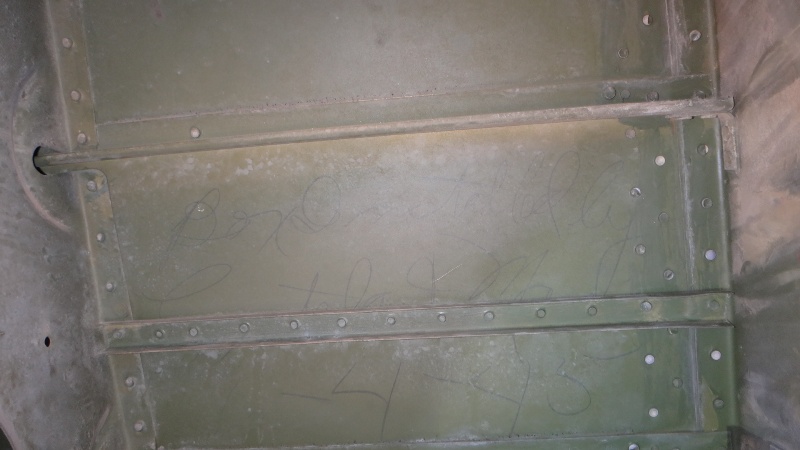
Ricky rebuilds the cylinder and cleans up the pulley brackets. He also replaces some pulleys and reprocesses the bearings on others as needed.
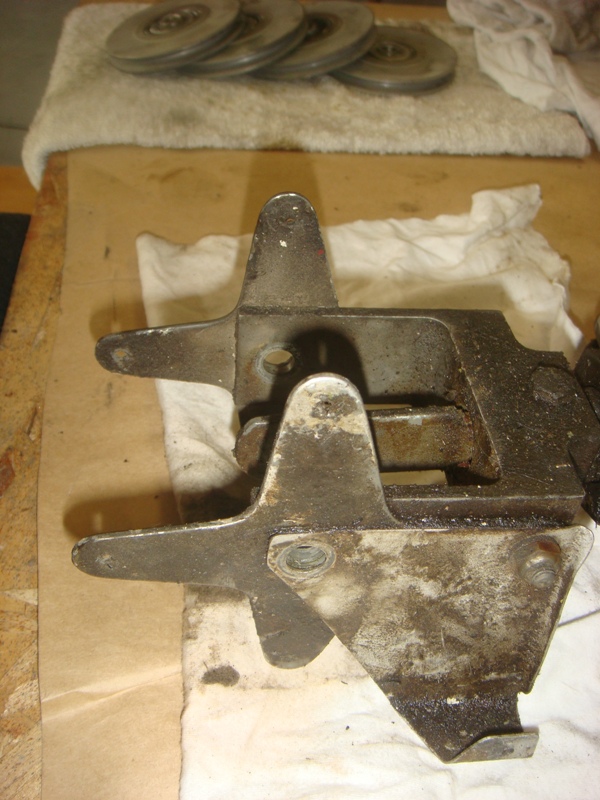
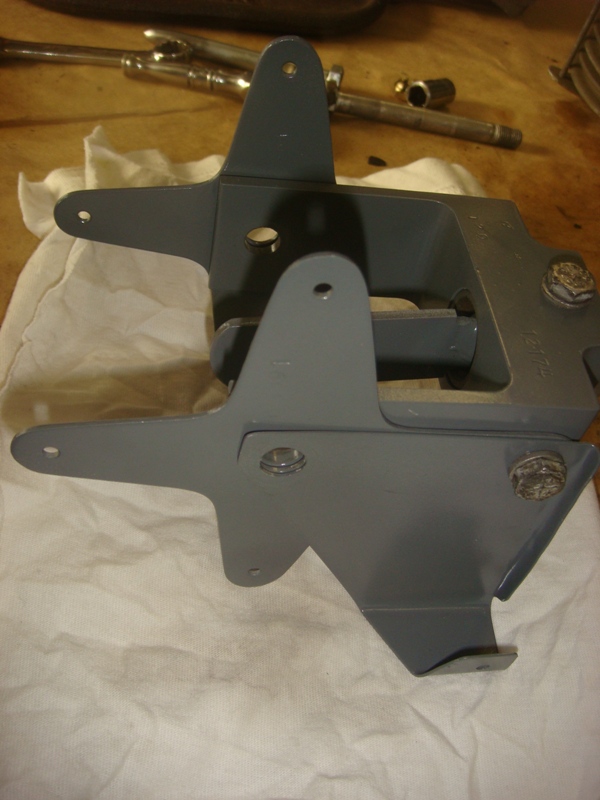
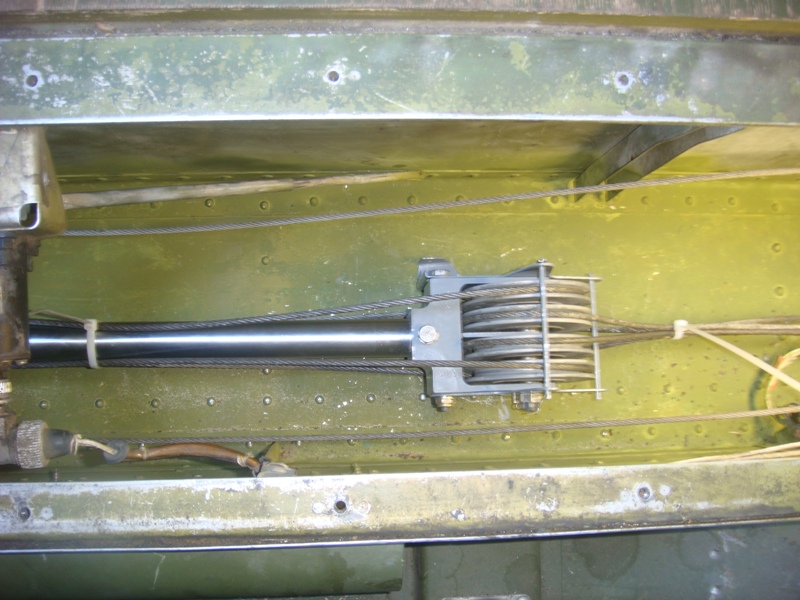
Ricky rebuilt the flap cylinder and was able to replace some of the parts with new ones that came from a large stash of PV parts we had acquired early on. Its nice to have some spares available to keep the old gal up and running. The cylinder was pressure tested and went back in. Ricky re rigged the system (no easy task mind you!) and it worked beautifully. Awesome job Ricky, as usual. You da man!
Lots of work to keep a big old gal like this up and running. Thankfully we have some fantastic volunteers that pitch in to help make it happen. We all appreciate the help we have but if any of you want to come out and lend a hand please do so. Its a lot of work but a lot of fun too. We also appreciate any monetary contributions too.
Thanks again!